Shaping the future together
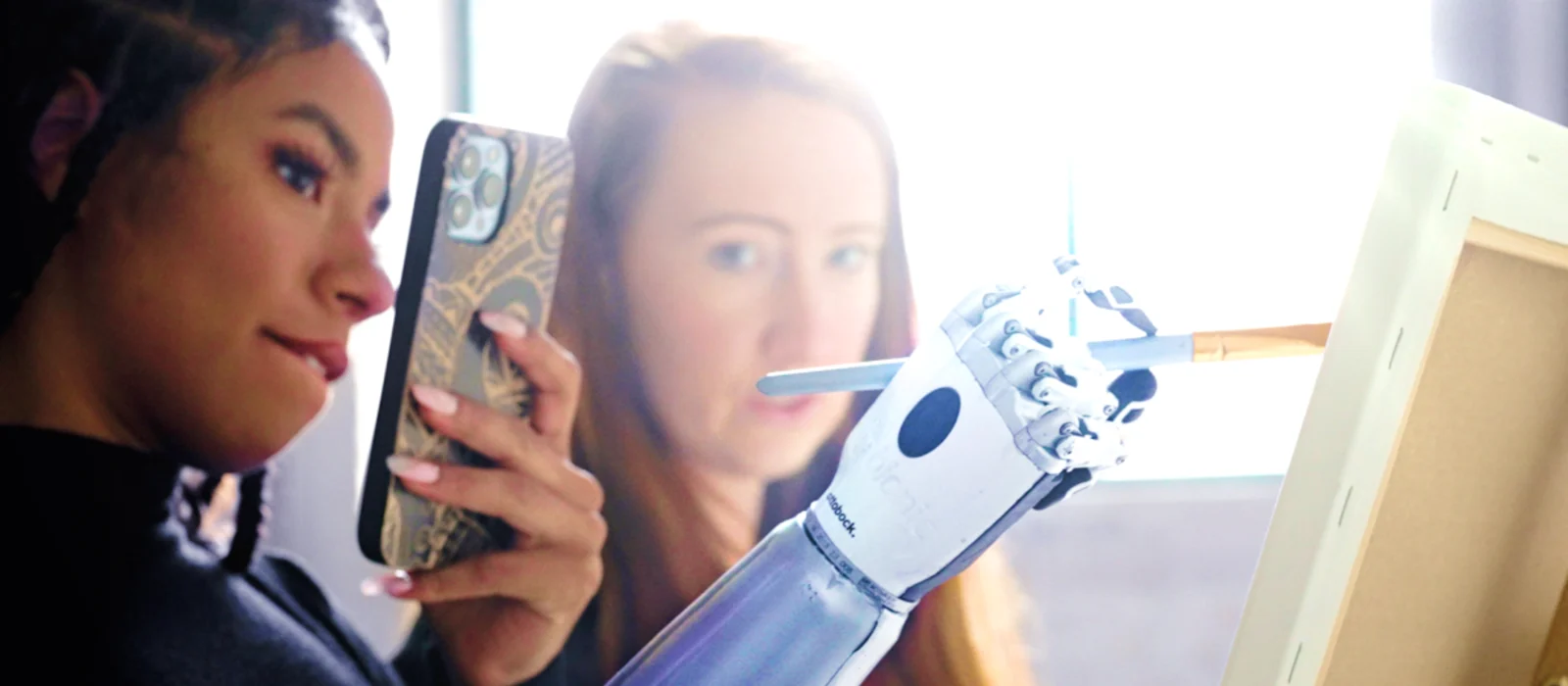
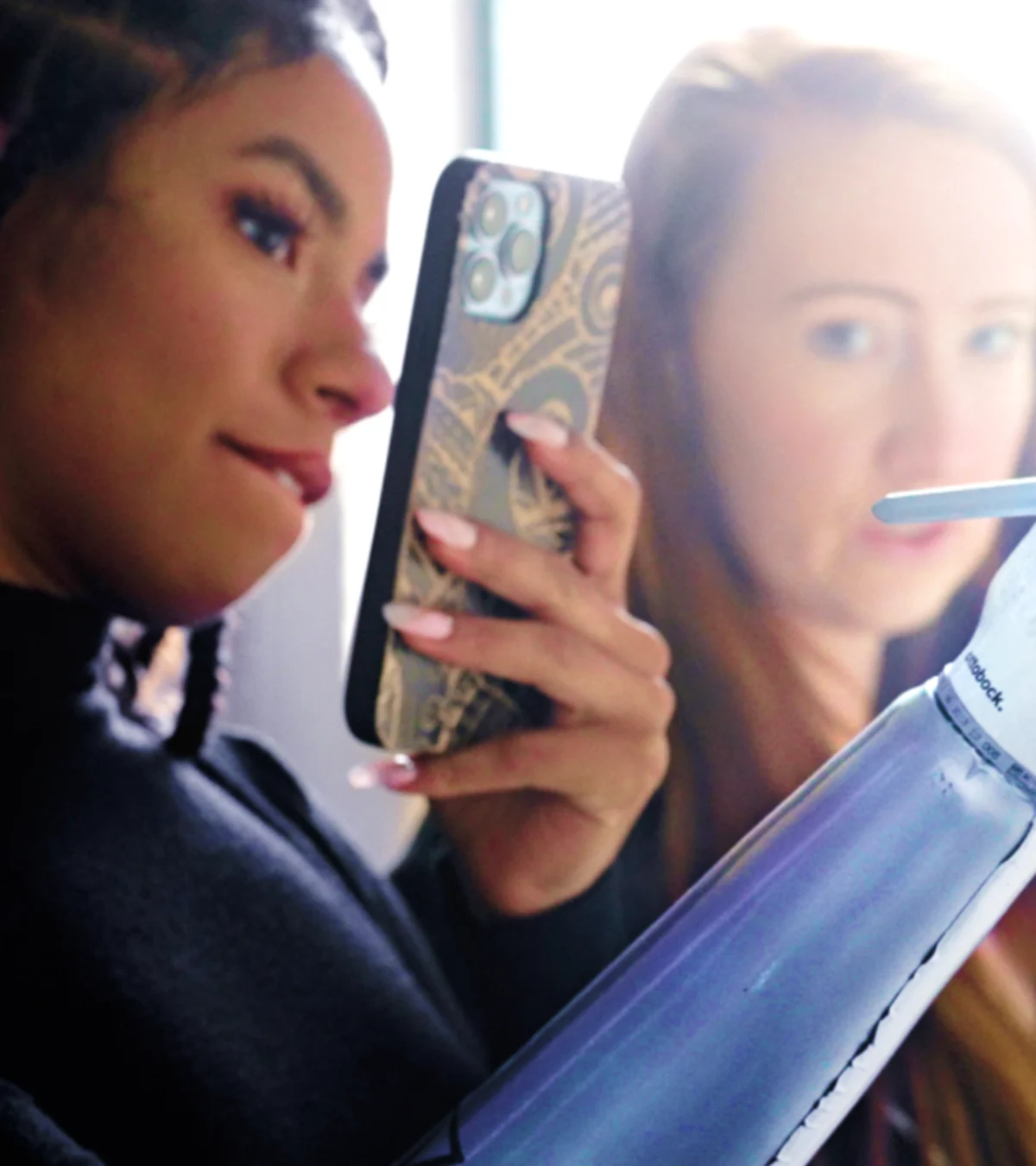
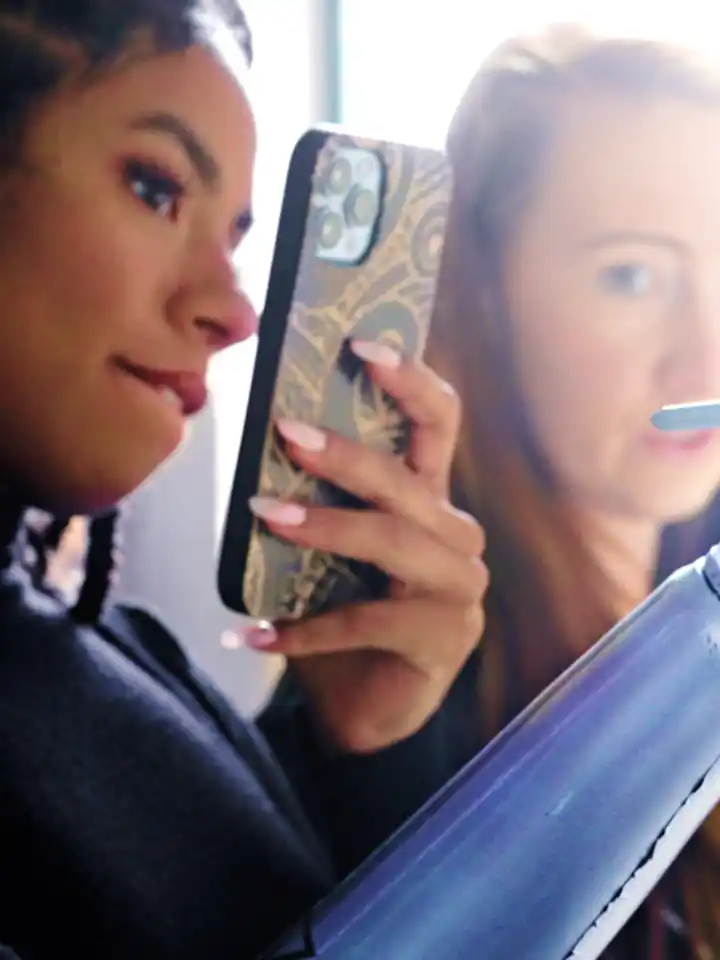
Shaping the future together
From innovative manufacturing technologies and 3D printing to digital supply processes, smart sensors or artificial intelligence. Digitalisation is opening up new expectations and opportunities in orthopaedic technology. We combine passion for craftsmanship with intelligent, digital technology. Today, we can already implement the entire lower limb treatment process digitally – from a 3D scan of the residual limb to the digital modulation of the prosthetic socket for 3D printing in our iFab (individual fabrication), to transferring a 3D model from the check socket to the definitive socket with millimetre precision.
Artificial intelligence supports the treatment process along the entire patient journey. The goal in using AI is to simplify processes for O&P professionals, further optimise treatment for their patients and improve product quality. Assistance systems equipped with AI, for example, facilitate communication with the paying party, AI compensates for the shortage of skilled workers in the manufacturing process, and intelligent support for users helps to offer maintenance and repair services at an early stage.
Cloud solutions give orthopaedic technology businesses a comprehensive view of the machines in their workshop, from important information on work progress via push notifications on smartphones to reminders for maintenance. This reduces waiting times and downtime, for example, across all areas and locations. This gives O&P professionals more time to focus on their core business: providing patients with the best possible treatment.
So-called large language models support O&P professionals, for example in formulating arguments for the reimbursement of their patients’ devices. Artificial intelligence analyses the gait pattern of self-recorded patient videos, without any sensors or markers, and outputs them as simple biomechanical data to illustrate the effects of treatment.
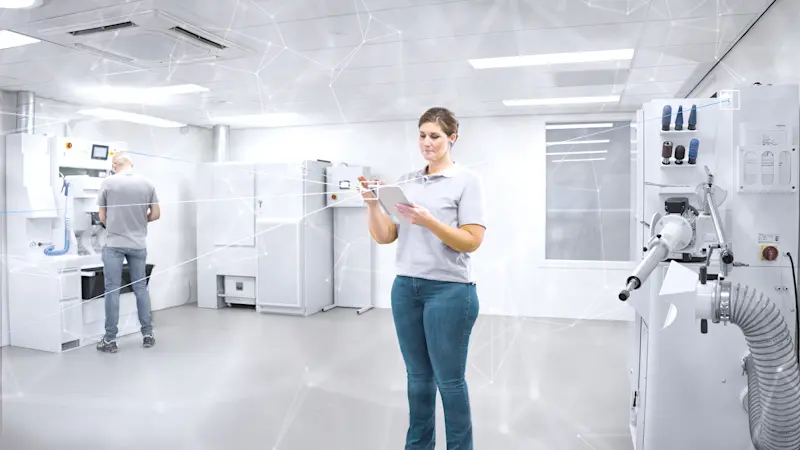
Putting people at the centre of a digital healthcare system
We want to accompany users throughout their treatment journey and make it as straightforward as possible. As a digital ecosystem, the lifelounge will link everyone responsible for the quality of life of people with disabilities, allowing users to find hospitals, medical supply companies and meet experts from the fields of orthopaedics and medical technology. This results in a positive interaction between all parties.
Among other things, we use a variety of cloud solutions and artificial intelligence to give us a comprehensive overview of users so that we can provide them with targeted, personalised support at every stage of their treatment.
Georgia NäderWith the help of digitalisation, the lifelounge is continuing to put the focus on users and their needs, and better enable them to live their lives the way they want to.
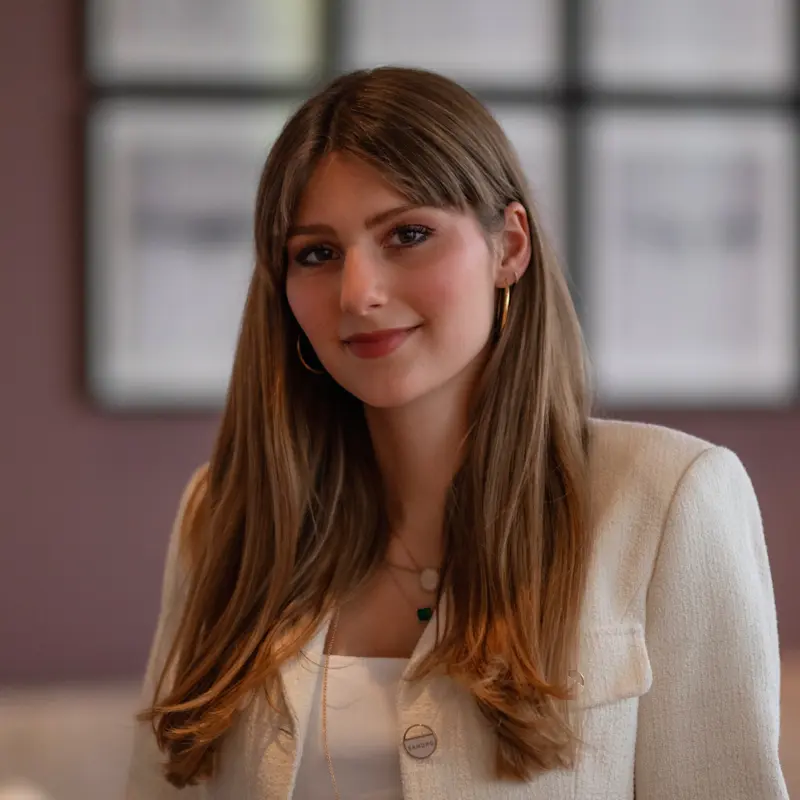
How innovative technologies are changing prosthetics
Ottobock introduced the C-Leg – the world’s first leg prosthesis to be controlled by microprocessors – back in 1997. The experiences we gained in the process led to the introduction of the Genium in 2011. This solution simulates a natural, physiological gait almost perfectly with the help of microprocessors, microsensors and micromotors. This enables users to move with maximum safety, even on difficult surfaces.
Combined advances in computer, sensor and motor technology mean that users can now use the prostheses for running, cycling and swimming. Users can simply select the various modes; an app on their smartphone is one way of doing so. This demonstrates how digital transformation is opening up new opportunities. At the same time, it also creates new requirements – so a special coating on Ottobock’s bebionic hand prosthesis now makes it easy to interact with touchscreens on mobile phones or tablets.
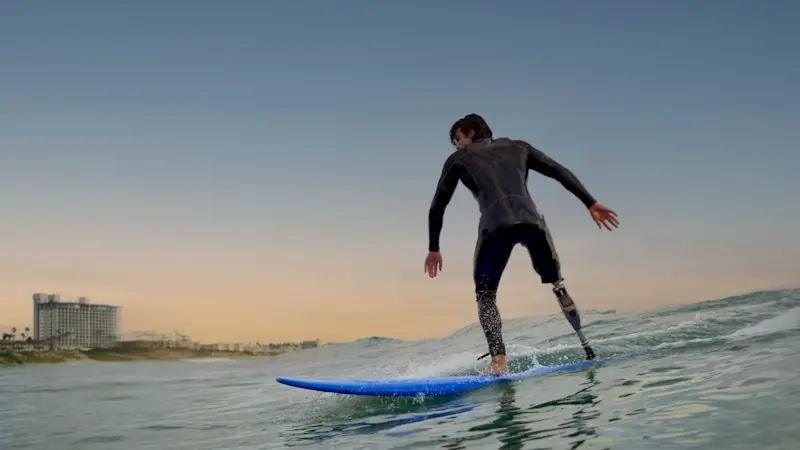
Artificial intelligence (AI) for intuitive movements
How does a hand prosthesis know when to flex a finger and type on a keyboard? In the past, people with an amputation had to spend considerable time learning to give their prosthesis complex signals via muscle contractions. Today, prostheses can learn from their users. Thanks to electrodes that capture biosignals in the residual forearm and artificial intelligence, Ottobock prostheses are able to identify how the user wants to move and automatically assign these signals to the correct hand movement.