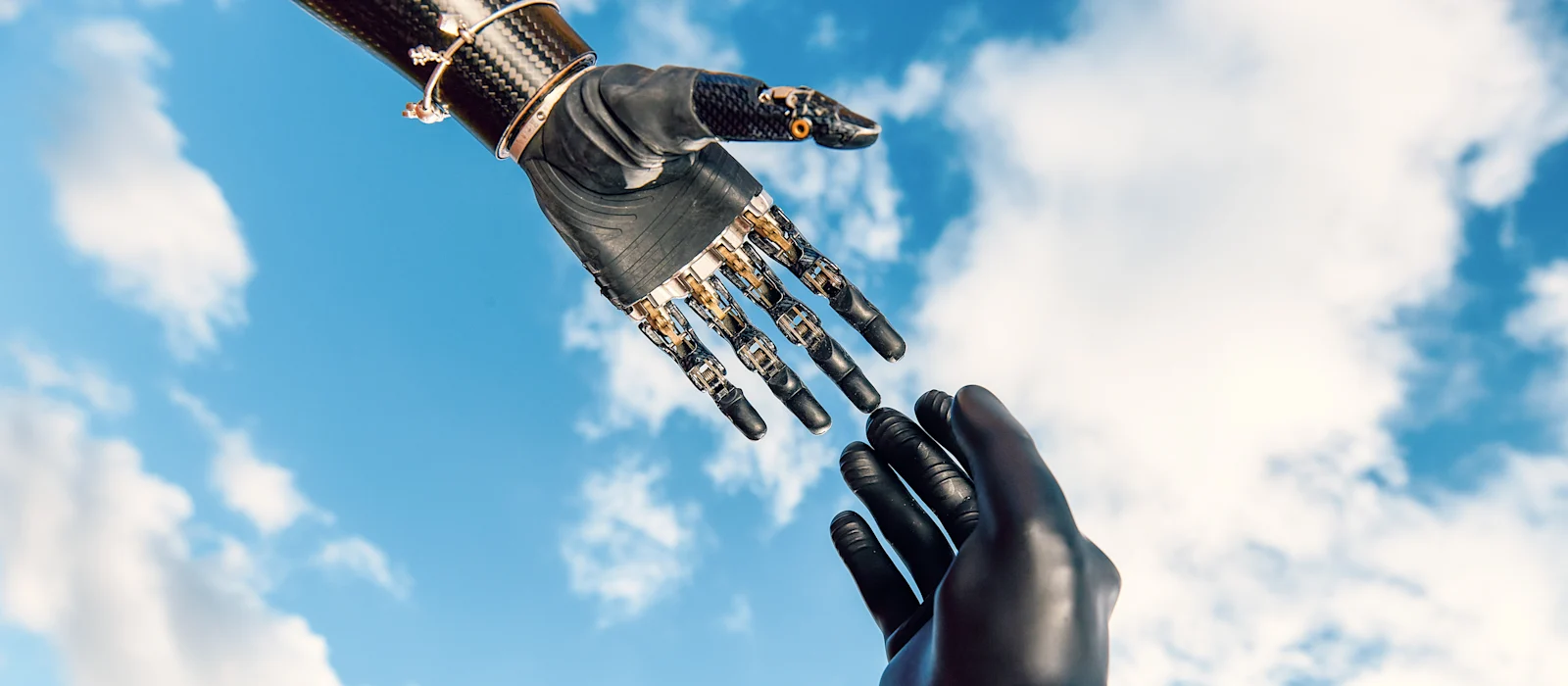
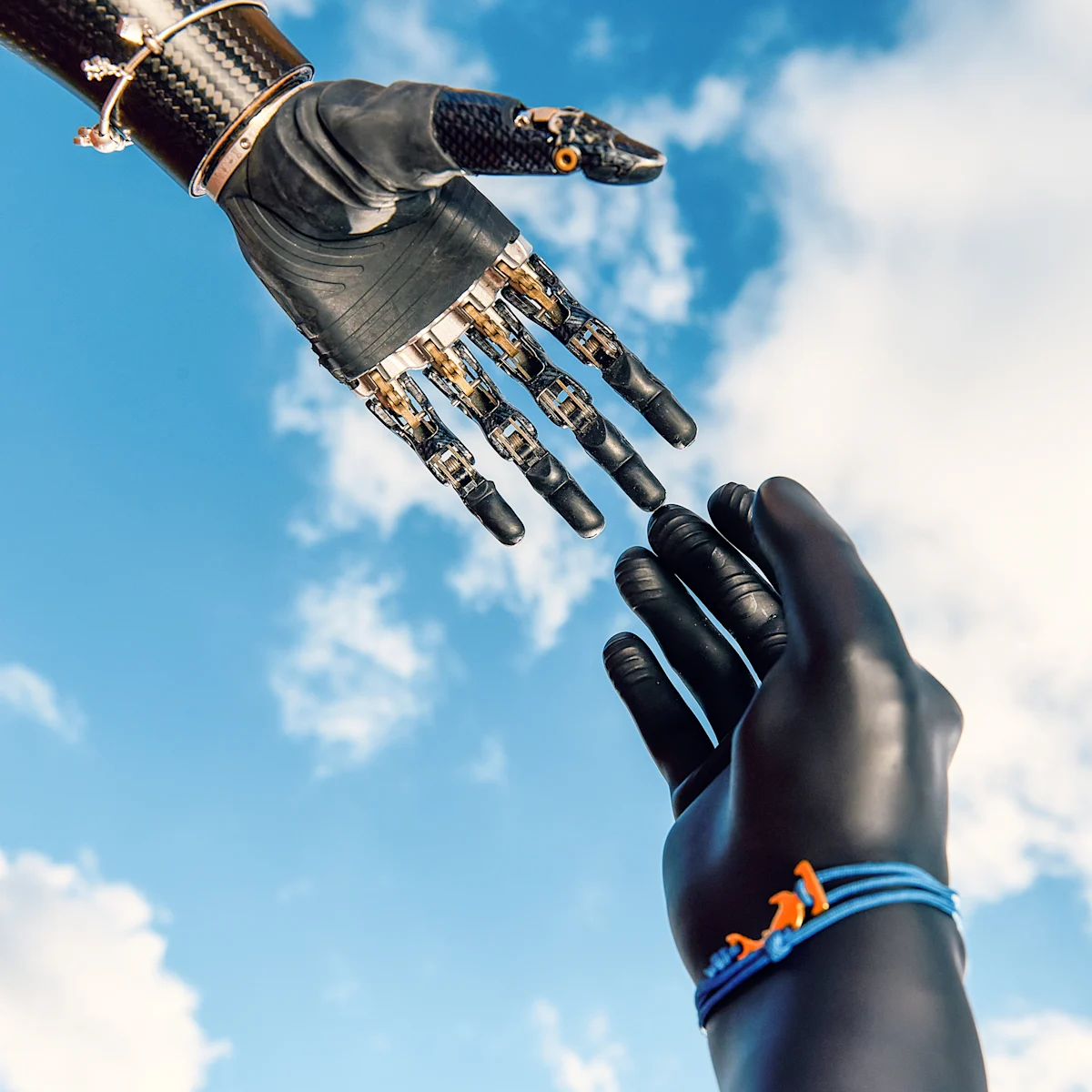
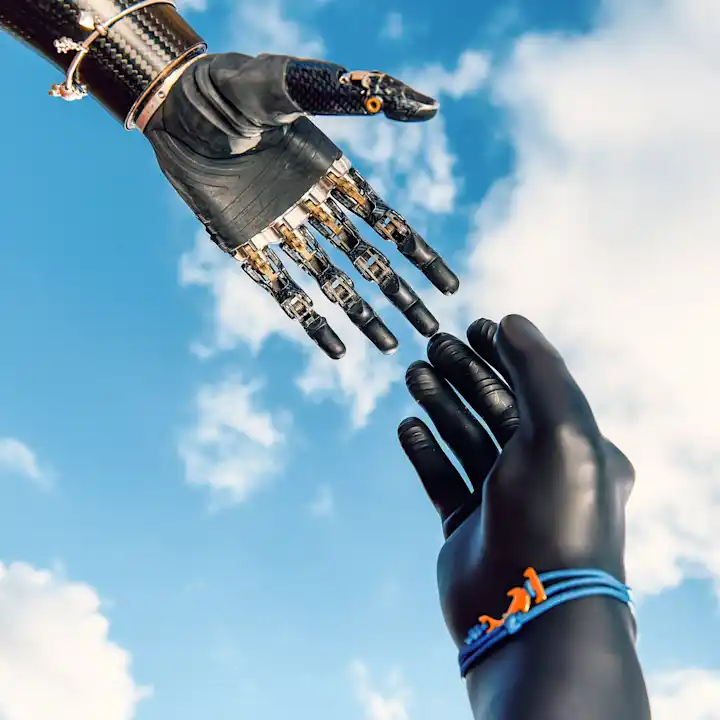
Intelligent hand prostheses
Using artificial intelligence to detect and automatically execute hand movements
Using artificial intelligence to detect and automatically execute hand movements
How does a hand prosthesis know when to flex a finger and type on a keyboard? In the past, people with an amputation had to spend considerable time learning to give their prosthesis commands through targeted muscle tensing. Today, prostheses learn. With the help of artificial intelligence, a prosthesis recognises desired hand movements and executes them automatically.
The prosthesis that learns from humans
Myoelectric impulses initiate movements in the muscle, such as in the hand. Intelligent hand prostheses make use of this: Electrodes in the prosthetic socket absorb the muscle impulses, and an artificial intelligence (AI) learns which movements prosthesis wearers want to perform, such as reaching for a spoon.
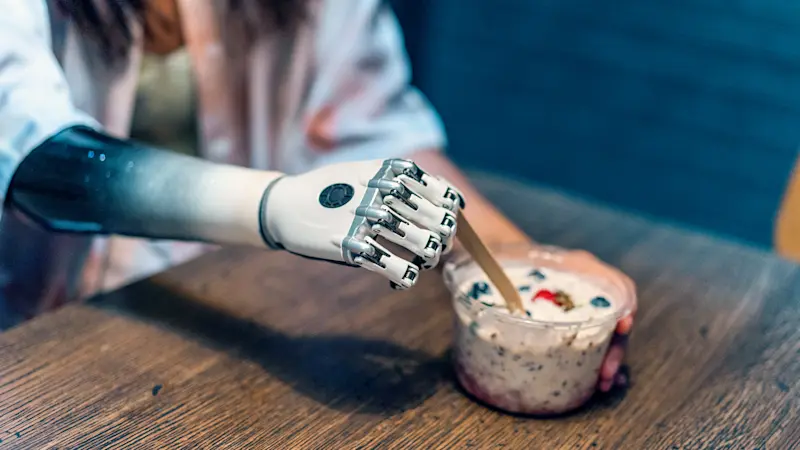
Hand movements without thinking twice – just like with a real hand
Wolfgang lost his right arm in a work accident. Using Myo Plus prosthesis control, his right hand can now perform the same movements as his healthy hand. In his own words: “I simply think about performing the movement with my phantom hand, and the prosthesis carries it out. It feels just the same as doing it with my healthy hand.”
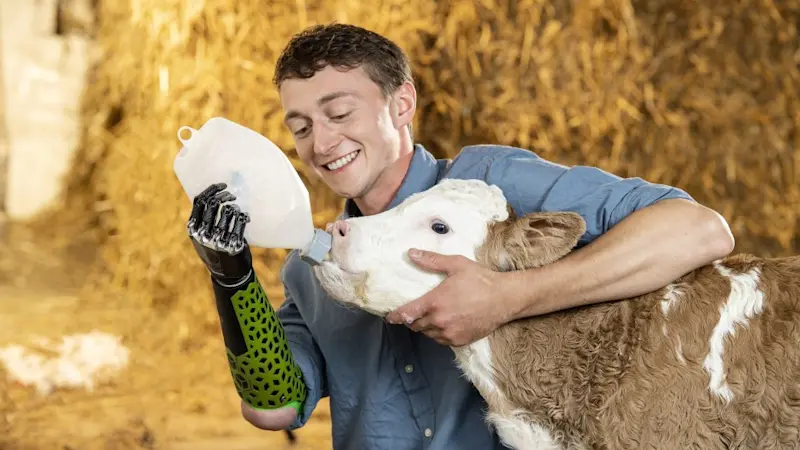
Recognising, saving and retrieving movement patterns
Myo Plus is Europe’s first prosthesis control device with pattern recognition. Eight electrodes in the prosthesis control device measure the movement patterns of muscles in the residual forearm and assign them to certain hand movements or grips. When the user reaches for a bottle of water, for example, the Myo Plus prosthesis control device recognises the associated movement pattern and automatically gives the prosthesis the command to perform the respective grip or rotation.
Users control the prosthesis learning process themselves
After the initial fitting by an O&P professional, patients can independently manage the prosthesis control device using an app. The app visualises the measured movement patterns. This allows the patient to practise subconsciously accessing each precise pattern. The initial training on how to use the new control device only takes a few days. The greatest challenge users face is the similarity between individual patterns. Due to the fact that many hand movements differ only by the slightest nuance, Myo Plus has to recognise and correctly assign a huge number of different patterns. As soon as communication between the user and the control device has been established, you can save any progress via the app and thus make your own adjustments.
Myo Plus pattern recognition is compatible with all Ottobock myoelectric hand prostheses.
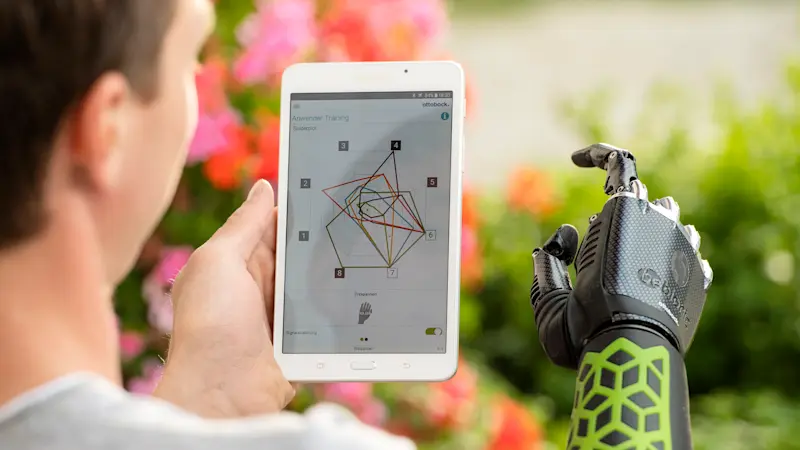
The most lifelike prosthetic hand
The bebionic hand is also revolutionising the lives and abilities of people around the world who have a malformation or amputation of the upper limbs. Its strength lies in its broad range of grip patterns. Among other things, prosthesis wearers can extend their index finger to use the keyboard of a PC or laptop as well as the keypad on a phone. The hand prosthesis is available in three different sizes.
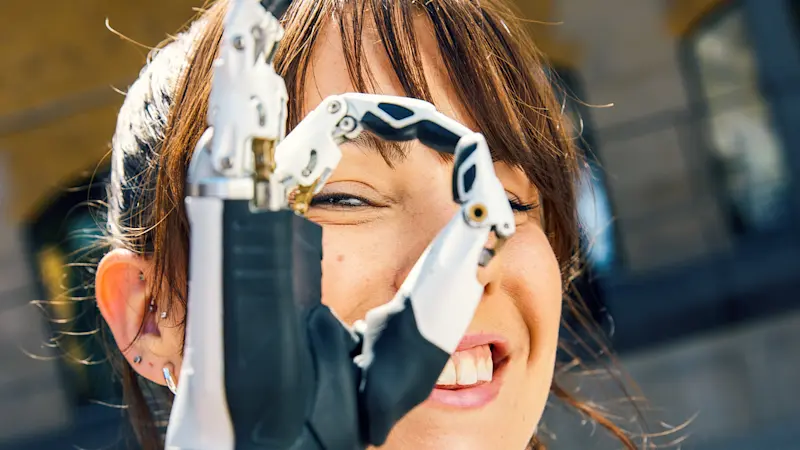
At a glance
Thanks to a selection of 14 grip patterns and hand positions, the multi-articulating hand is the perfect match for the day-to-day challenges of the digital world of work.
The bebionic hand automatically senses when a gripped item begins to slip from the hand. The auto-grip function then adjusts the grip accordingly to prevent the object from falling.
Individual motors in each finger allow the hand to move and grip in a natural, coordinated way. The motors are positioned to optimise weight distribution. This makes the hand lighter and more comfortable to wear.
Thanks to the proportional speed control feature, the prosthesis wearer can even manage tasks requiring a high level of precision, such as holding an egg or polystyrene cup.
The bebionic hand has passively movable fingers. These yield when they brush against people or unintentionally bump into objects and fold away comfortably to protect the mechanics of the hand.
Thanks to a digital interface to Myo Plus pattern recognition, users can fully take advantage of the potential of the bebionic.

Living with a prosthetic hand
More than 270,000 people around the world wear an arm prosthesis. They overcome challenges, achieve success and live their lives. Using the hashtag #NeverStopReaching, arm prosthesis wearers are sharing their personal experiences on social media and taking their community with them on their journey. At the same time, Ottobock uses its website “bionic life – living with an arm prosthesis” to provide individuals with a central point of contact for obtaining information, exchanging ideas and networking.
The people behind the movement
International influencers, including Gina, Bebe and Cameron, are the force behind #NeverStopReaching.
Natural appearance

It’s much easier to recognise a prosthesis as part of yourself when natural motion patterns are possible and the design is just right. Both of these factors were paramount for Ottobock during the development of the Michelangelo hand prosthesis.
What's behind it
Muscle signals from the residual arm control two drives: the main drive for the gripping movement and gripping force and a separate thumb drive – this enables seven different hand positions.
The thumb, index finger and middle finger are controlled actively, while the ring finger and little finger passively follow the movements. Thanks to this functionality, the Michelangelo enables gripping movements that every person uses again and again in their work as well as their free time. These include, for example, gripping a glass from the side, holding flat objects such as paper, supporting a plate on your open hand or clasping a pen.
A mechanical wrist joint supports the movements. The joint can be flexed and extended as well as rotated inwards and outwards, and it also mimics the natural behaviour of a relaxed wrist.
The fingers are made of both soft and hard materials, and thus based on the natural hand in detail. Suitable for everyday use, the compatible prosthetic gloves have a multilayer structure and come in six different shades. Coloured fibres on the inside simulate the natural vein structure of the human hand. For those who wish to show off their modern arm prosthesis, a transparent and a black prosthetic glove are available as well.
Intuitive control of the upper arm prostheses
Targeted muscle reinnervation has developed into a proven treatment method following amputation of the upper arm or a shoulder disarticulation. A new function is surgically assigned to the nerves in the residual limb that previously controlled the arm and hand. The nerves are removed from the surrounding tissue and connected precisely to muscles in intact areas of the body. They can then grow into the pectoral muscle, for example. This allows patients to control their subsequent arm prosthesis using “thought signals”.
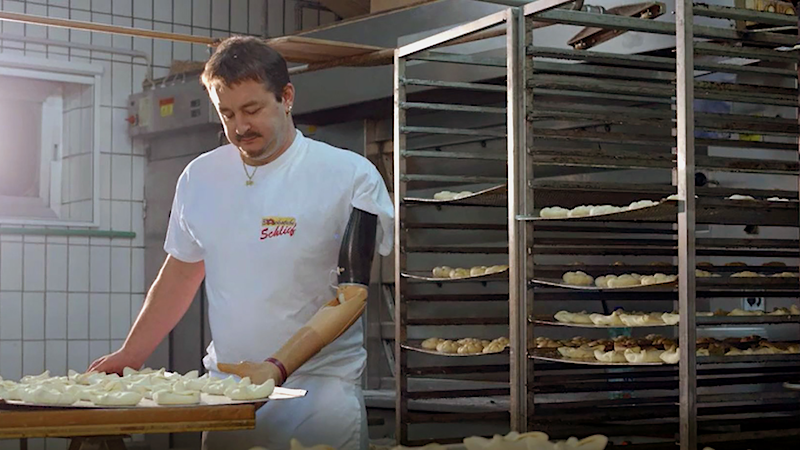
Signals from the musculature control the hand
When users imagine moving their phantom arm, the nerves transmit the signals to the new target musculature so that it is tensed. This results in electric signals in the millivolt range, which are measured by electrodes in the prosthetic socket. A miniature computer analyses the signals and translates them into the intended movement. If the user thinks of making a fist, for example, or closing their hand, the corresponding muscle is activated and the associated signal closes the prosthetic hand.
For the first time, TMR treatment also makes it possible to move several joints at the same time. The TMR arm prosthesis is equipped with up to six electrodes for this purpose, in contrast to conventional myoelectrically controlled prostheses, which are controlled by just two electrodes. This lets the user control up to six movements with separate muscle signals – and gives them significantly better control over the prosthesis. TMR allows the user to intuitively make faster, more precise movements with the arm prosthesis.
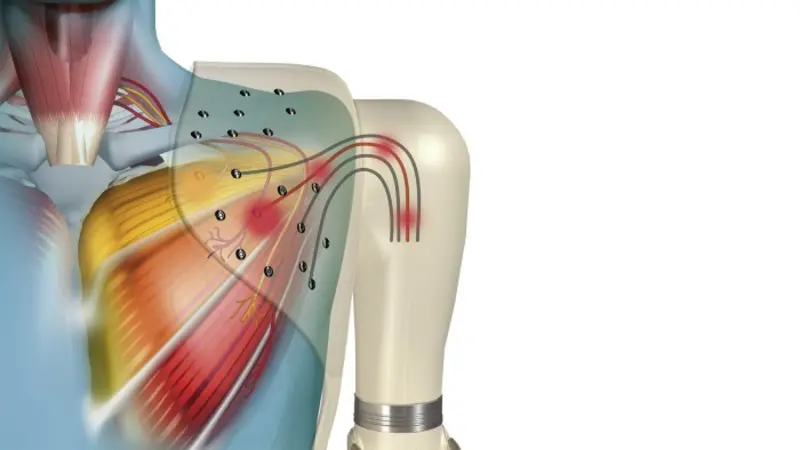
The TMR treatment process
Treating a patient with a TMR arm prosthesis is considerably more complex and intensive than treatment involving a conventional prosthetic device. The entire process, from the operation up to the definitive fitting, requires close cooperation between the surgeons, O&P professionals and physiotherapists. Because this process is highly tailored to the patient as an individual, it can take up to two years.
Interdisciplinary cooperation
Patients receive therapeutic preparation for the operation as well as an individual rehabilitation programme afterwards. The most significant phase is known as “signal training”: This complex motor training ensures that the patient learns to adequately and selectively activate the newly innervated muscles. Based on this training, the O&P professional then determines the ideal position for the electrodes. Before the final prosthesis can be fitted, users first try out a number of therapy and training prosthetic sockets. They also gradually become accustomed to the weight of the prosthesis. Once the O&P professional has found the optimal settings, the definitive socket is fitted. Physiotherapists support the patient during the further process of learning to use the prosthesis. Regular follow-ups with the interdisciplinary team ensure the long-term success of TMR treatment.
Ottobock’s new upper arm solution approach
Until 2022, Ottobock offered the Myo Plus prostheses only for the forearm. There are significantly fewer myoelectric signals in the upper arm that can receive muscle impulses. Opening and closing, inward and outward rotation of the hand, and flexing and extending the elbow joint all happen in the forearm. If the arm is missing above the elbow, these movements must therefore be replaced and controlled with a great deal of effort.
Ottobock presented its approach to this for the first time atOTWorld 2022 in Leipzig: Myo Plus TH – a prosthesis control device for the Dynamic Arm that learns and intuitively carries out the desired movements in the upper arm using artificial intelligence (AI) and pattern recognition. In the prosthetic socket itself, significantly more electrodes are used to detect muscle impulses with the Myo Plus TH control device.
A TMR operationafter an amputation is not a prerequisite for treatment with the Myo Plus TH – but it offers significant added value: surgeons connect nerves that used to transfer signals to the natural arm to residual muscles. This allows the prosthesis to have more control signals. The combination of TMR and Myo Plus TH therefore shows great potential for increasing the treatment quality.
Contact persons
Additional topics
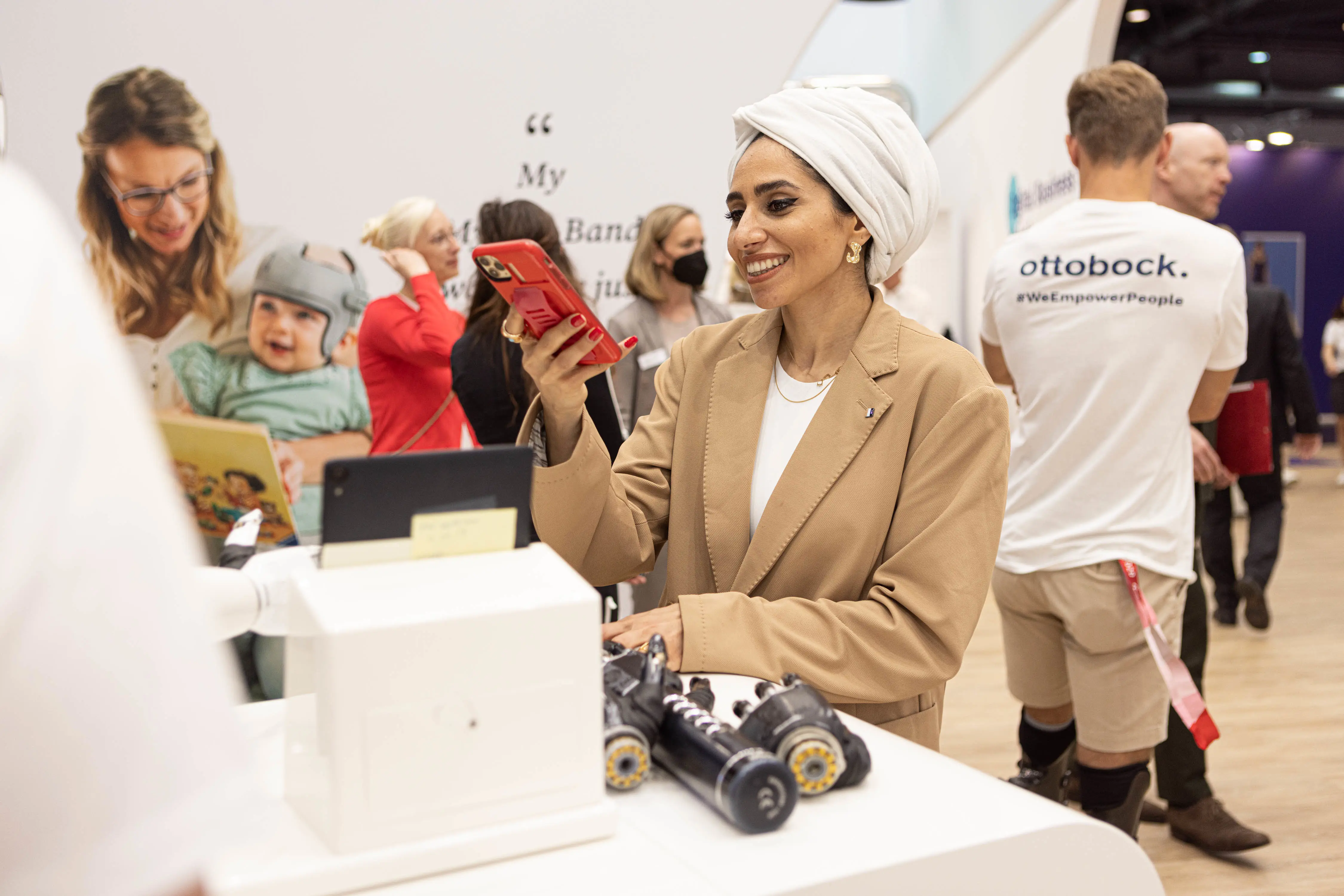
Media information
Would you like to know more about our product highlights? Do you need high-resolution images for your publication? We have compiled product information and images for journalists here.
Would you like to know more about our product highlights? Do you need high-resolution images for your publication? We have compiled product information and images for journalists here.
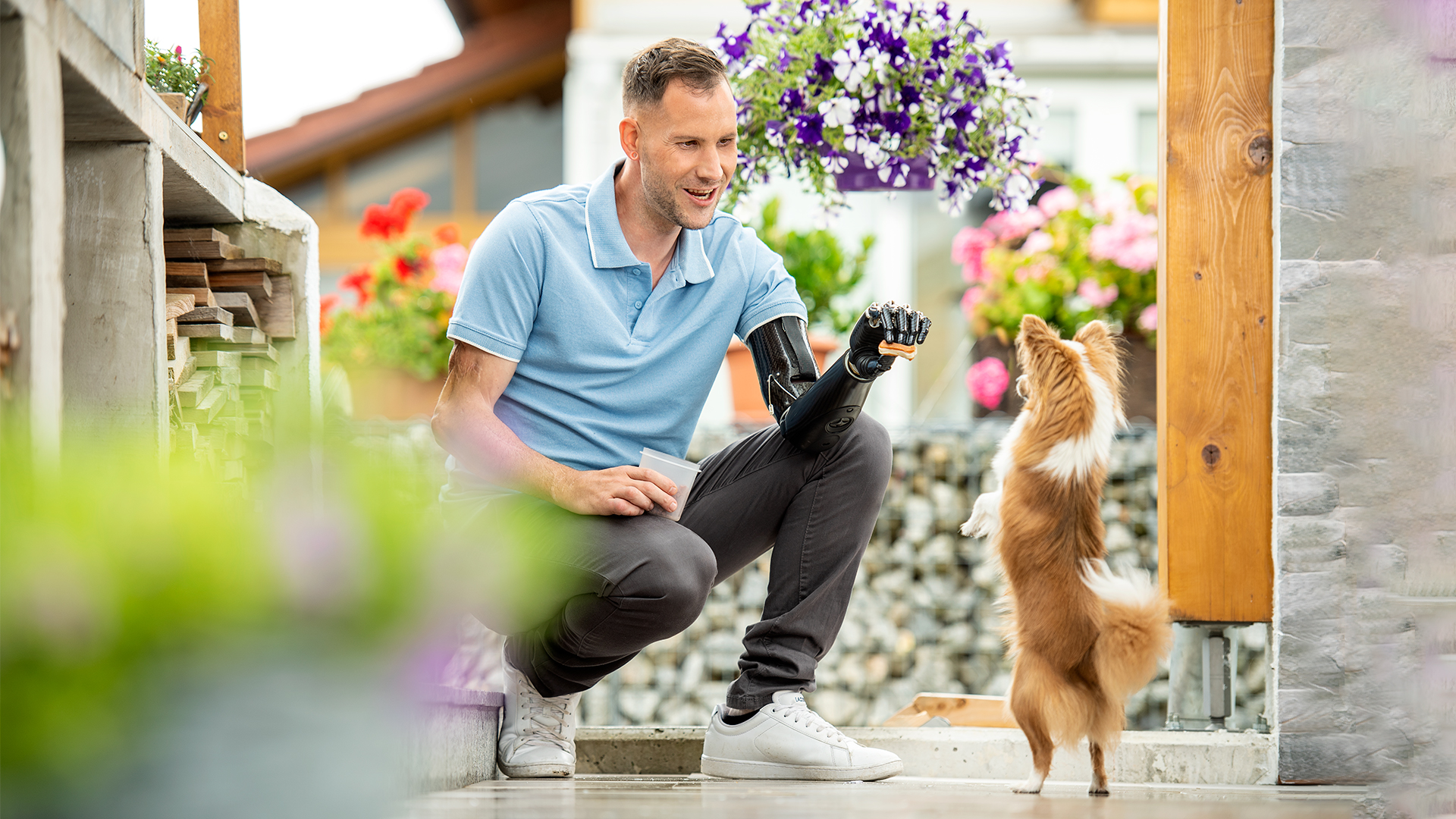
Innovations for people
We have been conducting research for our users, patients and customers for more than 100 years – and setting new standards in medical technology with our intelligent solutions.
We have been conducting research for our users, patients and customers for more than 100 years – and setting new standards in medical technology with our intelligent solutions.
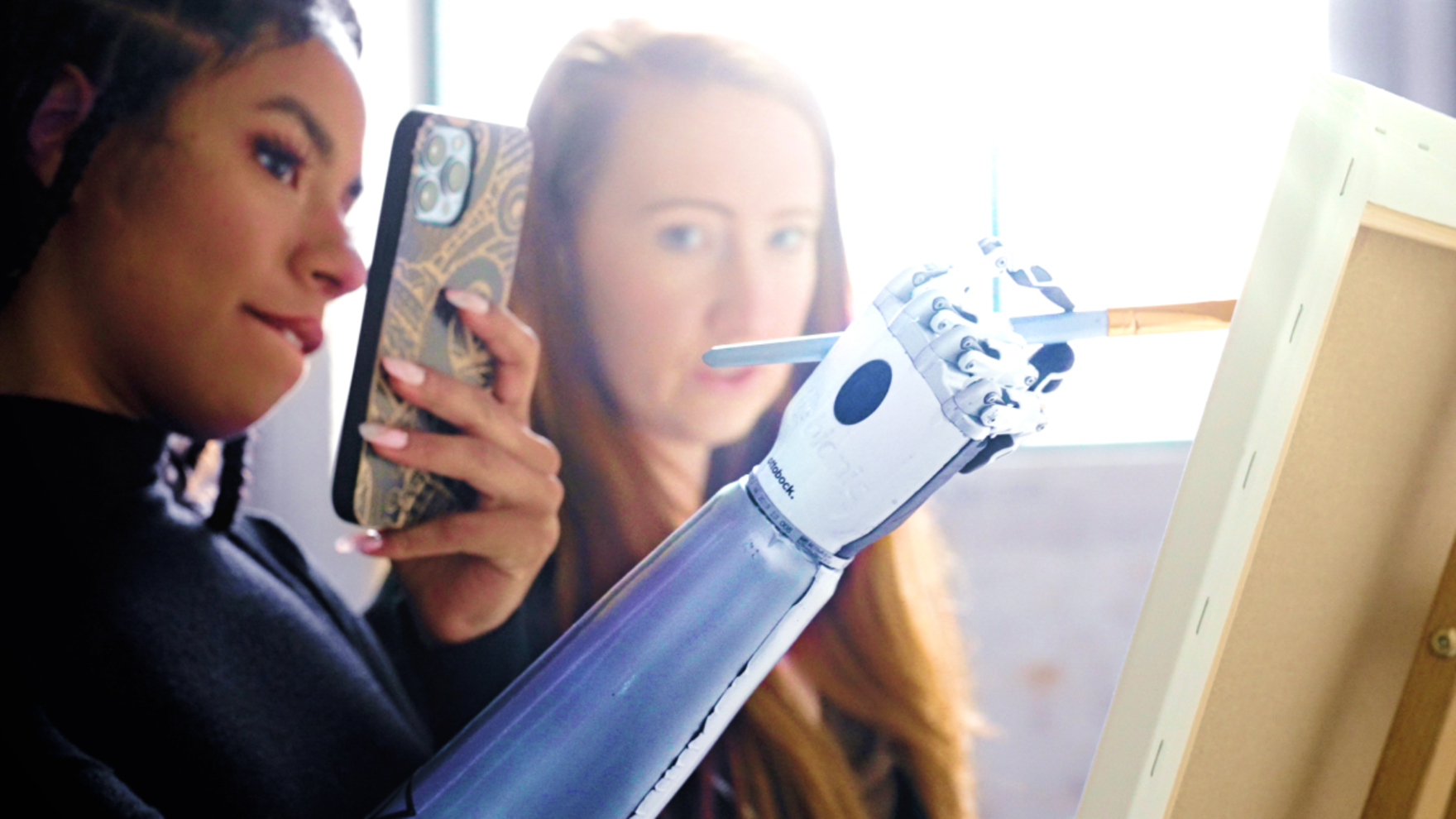
The future of orthopaedic technology
Here’s how apps, smart sensors, microprocessors, 3D printers and 3D scanners help people with and without disabilities today: discover innovations from Ottobock.
Here’s how apps, smart sensors, microprocessors, 3D printers and 3D scanners help people with and without disabilities today: discover innovations from Ottobock.
3 results out of 3