“I can switch quickly in a matter of seconds, so I’m ready for any situation.”
User story: Farmer Wolfgang Bauer controls his prosthesis intuitively with the Myo Plus pattern recognition
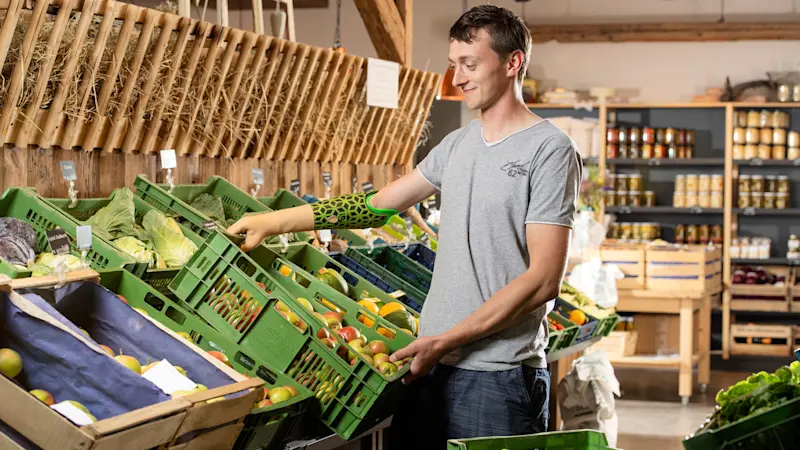
Tuesday, 19 March 2019
It’s early in the morning in the German region of Lower Bavaria. Future agricultural expert Wolfgang Bauer (23) has already been up and about for two hours. In the extensive buildings on his parent’s farm, he brings fresh hay to the animals and changes their water. Just two years ago, this would have been impossible due to an accident Wolfgang had. His right hand got caught in a chopper while he was working. The bones, tendons and muscles were destroyed, and his hand could not be saved. “But I was lucky despite this misfortune. The paramedics took me to the nearest hospital specialising in hand surgery,” he recalls. “Looking back, that was the best thing that could have happened, because I had a prosthesis just five weeks after the accident.”
Hand movements without thinking twice – just like with a real hand
“Not having a prosthesis was simply not an option for me. Of course, I initially hoped that they would be able to save my hand. But it soon became clear that that wouldn’t be possible, and after a few weeks, you begin to understand what’s possible with prosthetics these days,” says Wolfgang. Since he received his first prosthesis, many things have happened. Today he uses a prosthesis that he can operate intuitively thanks to pattern recognition and the use of artificial intelligence. For example, when he wants to hold a glass, the prosthesis control recognises the muscle contractions in the residual limb of his forearm and translates them into hand movements with the myoelectric prosthesis. “I don’t even have to think about the control. It basically happens automatically within a second. Just like with a real hand.”
Automatic switching between grips and rotations
Whether Wolfgang is in the barn, playing billiards with friends or working in the office at the farm – his work and leisure time are marked by activities that require rapid switching between different grips or rotations of the wrist. “In the past, I always had to move a kind of switch with the other hand to change the grip or rotation. That’s not necessary anymore.
"Today, I just think about the grip I want to use, and the prosthesis control does the rest,” says Wolfgang, adding, “I now use the different grips much more often because it is faster and easier. While working at the computer, I can use the keyboard with the finger point or work with the mouse again. They are just small differences, but they have big advantages for me.”
The prosthesis learns from the user via an app
The initial adjustment of the prosthesis control is made by an O&P professional. The user can then continue the process on their own and make additional adjustments with an app.
“I always open the hand quickly and then go to the individual grips. That’s my approach.
It’s all done subconsciously, so I move very, very quickly,” says Wolfgang of the learning process with the Myo Plus pattern recognition. “It was also important to me that the control device works with various prosthetic hands. For light but varied work on the farm, I use the multi-articulated bebionic hand, for example, which lets me use many different grips to best effect. For heavy work where I need more strength, I use the Electric Greifer.” Wolgang’s only wish for the future is a prosthesis that can give him back his sense of touch.