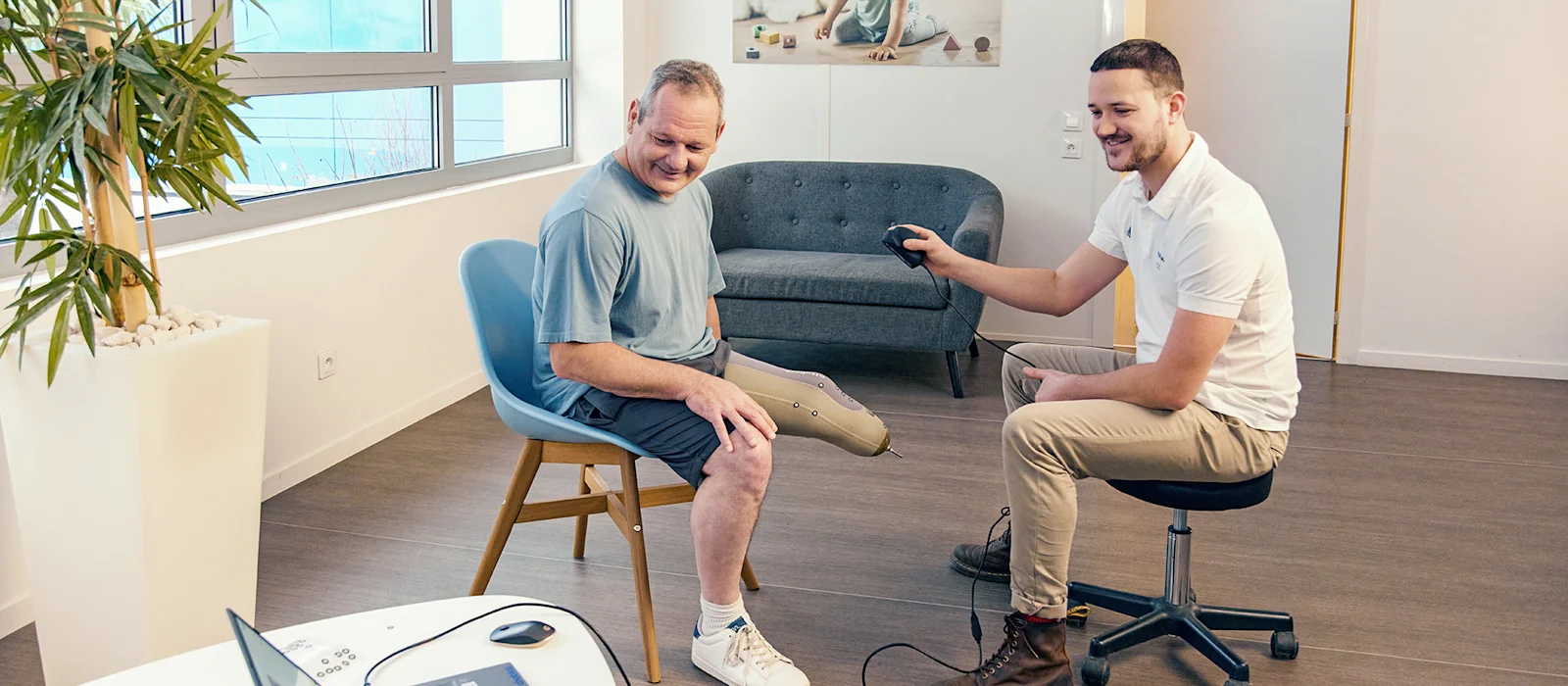
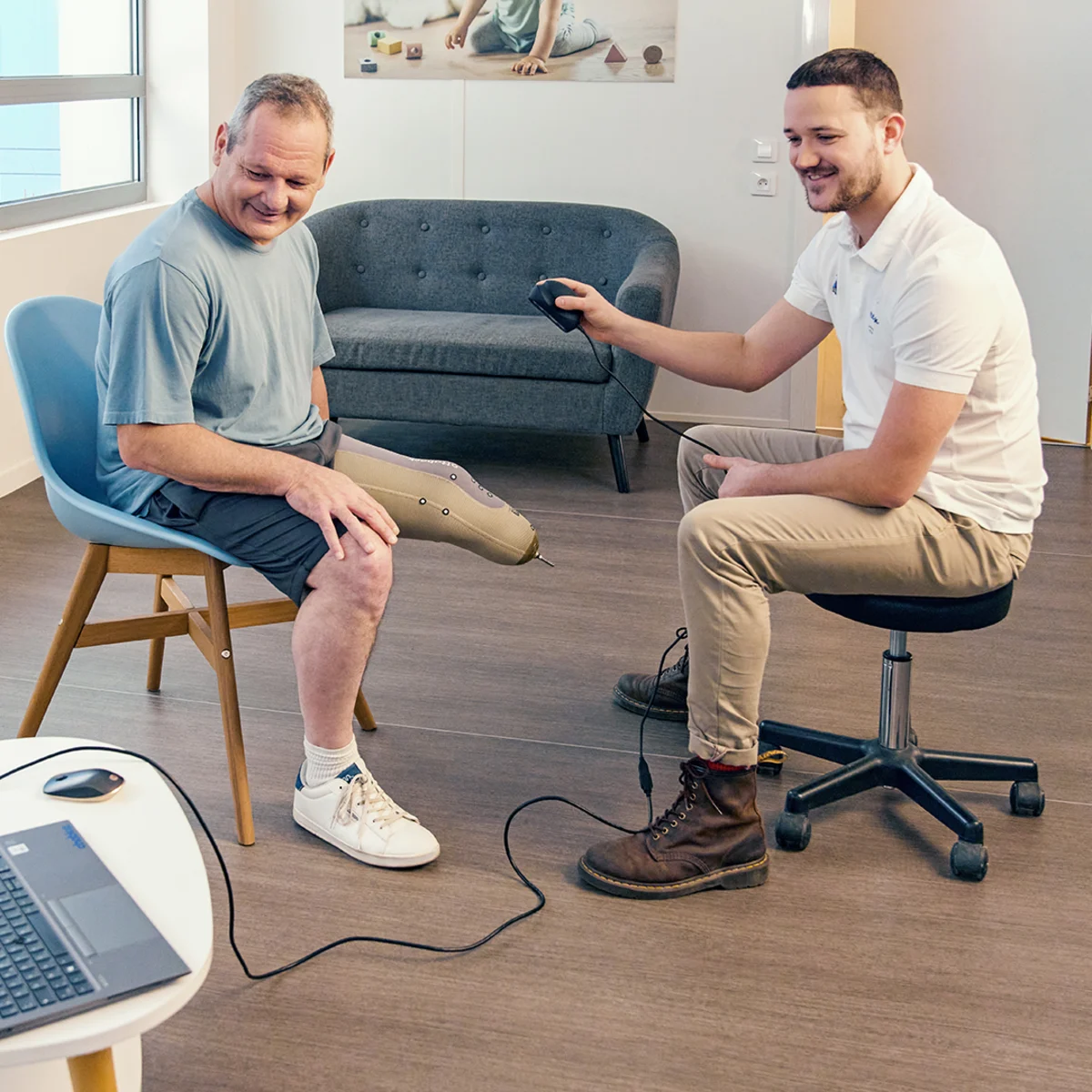
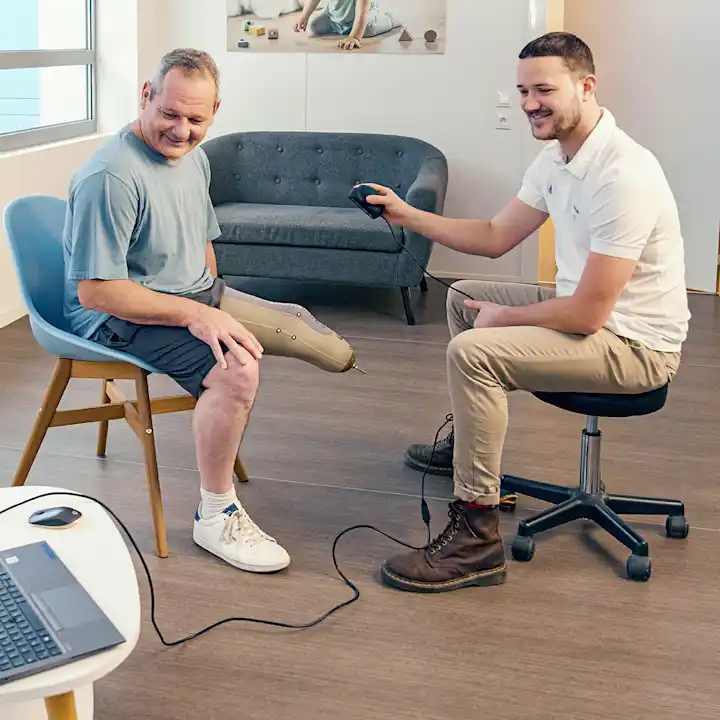
How 3D scanners and printers are revolutionising fitting for patients
Fast and customized production is the future of orthopedic technology. The iFab has digitized the complete fitting and production process.
Fast and customized production is the future of orthopedic technology. The iFab has digitized the complete fitting and production process.
Digital revolution of orthopedic technology
To this day, plaster casts are made in order to fit prostheses as effectively as possible. However, 3D scanners are a faster option that is more comfortable for the patient. Our iFab – short for “individual fabrication” – enables us to produce custom orthoses and prostheses quickly. O&P professionals scan a residual limb and process the data directly on a computer. Time that was once spent on manual work on the plaster cast – often a complex task – can now be channeled into the fitting process. The processed data are tested in a computer simulation and transferred directly to the milling machine and 3D printer. This minimises error sources. iFab digitalises the entire fitting and manufacturing process.
Uli Maier, O&P professionalAs an O&P professional, I was initially somewhat sceptical about digitalisation. However, I was won over when my first user reported that their 3D-printed liner actually fit better.
The four steps of digital fabrication
Digitising a craft
The digital ecosystem in iFab not only places a stronger focus on patients’ needs and interests during fitting. It also makes the related administrative processes easier for medical supply companies and orthopaedic technology businesses. Instead of making plaster models, they now transmit their data digitally via an online platform (the iFab Customer Centre). We support them as they make the transition to a plaster-free workshop and give them the digital tools they need to use our global Ottobock iFab fabrication sites as their extended workbench.
More time for people
Digitalisation eases the manual workload in orthopaedic technology. In return, there will be an even stronger focus on caring for patients. The iFab platform provides a crucial new intermediate step in patient fitting – namely, simulation. Using patients’ biometric data, a computer can now be used to check, even before it’s fabricated, whether the fitting solution will work as intended. This makes fabrication more precise, minimises potential errors and saves materials and time.
Higher quality fitting
At its site in Duderstadt, Ottobock is adding more intelligent innovations to its own process chain (scanning, modifying, 3D printing), making it more seamless. For example, the project team is developing special software solutions to scan and model human anatomy. It's also powering ahead to automate additive manufacturing and network the iFab hub in southern Lower Saxony with international digital fabrication sites.
The plan is to store data from individual digital fittings and also from the entire digital production chain in a central database in the future. Here, AI and algorithms filter out successful models and methods that can then be used to self-optimise devices and processes. Our vision is to create a seamless, digital fitting chain and 3D printing production chain that grows more intelligent over time, thus achieving even higher quality fittings.