Futuring
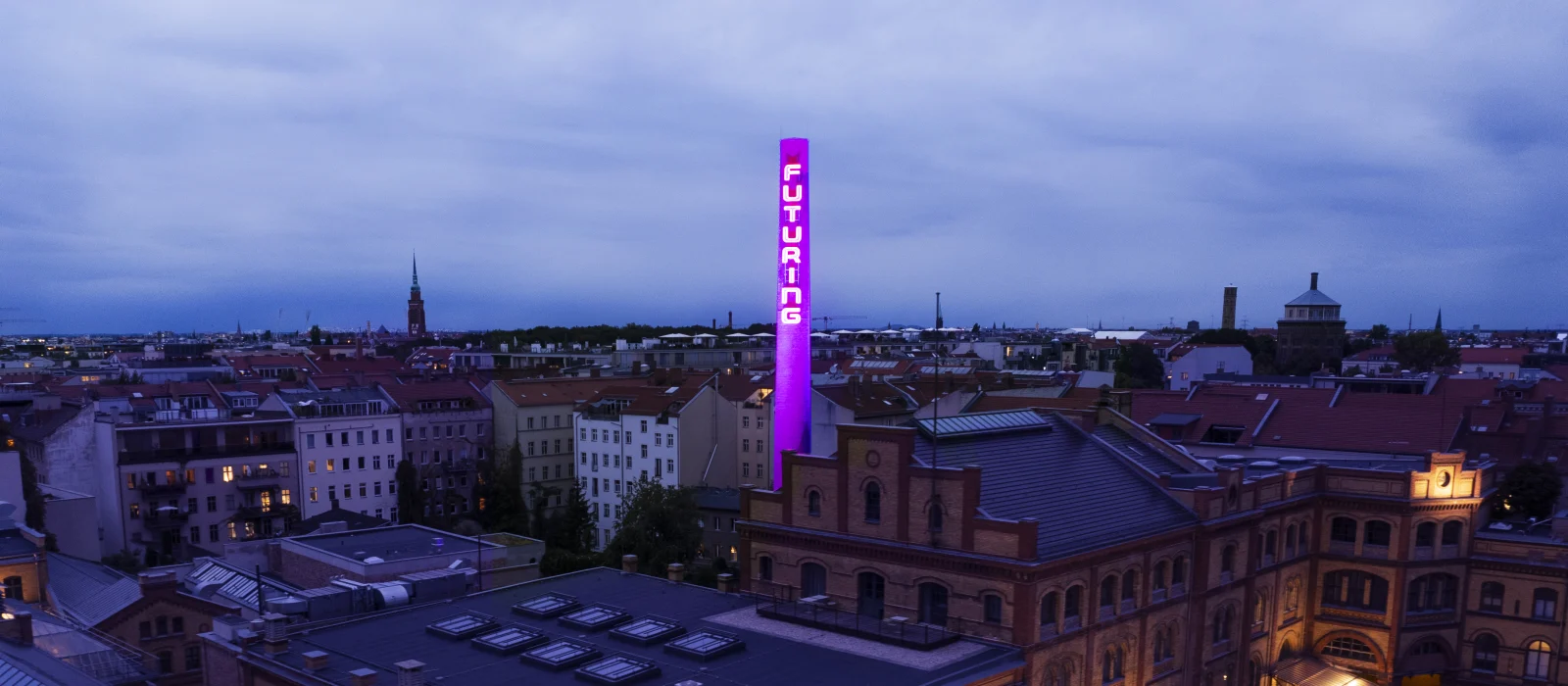
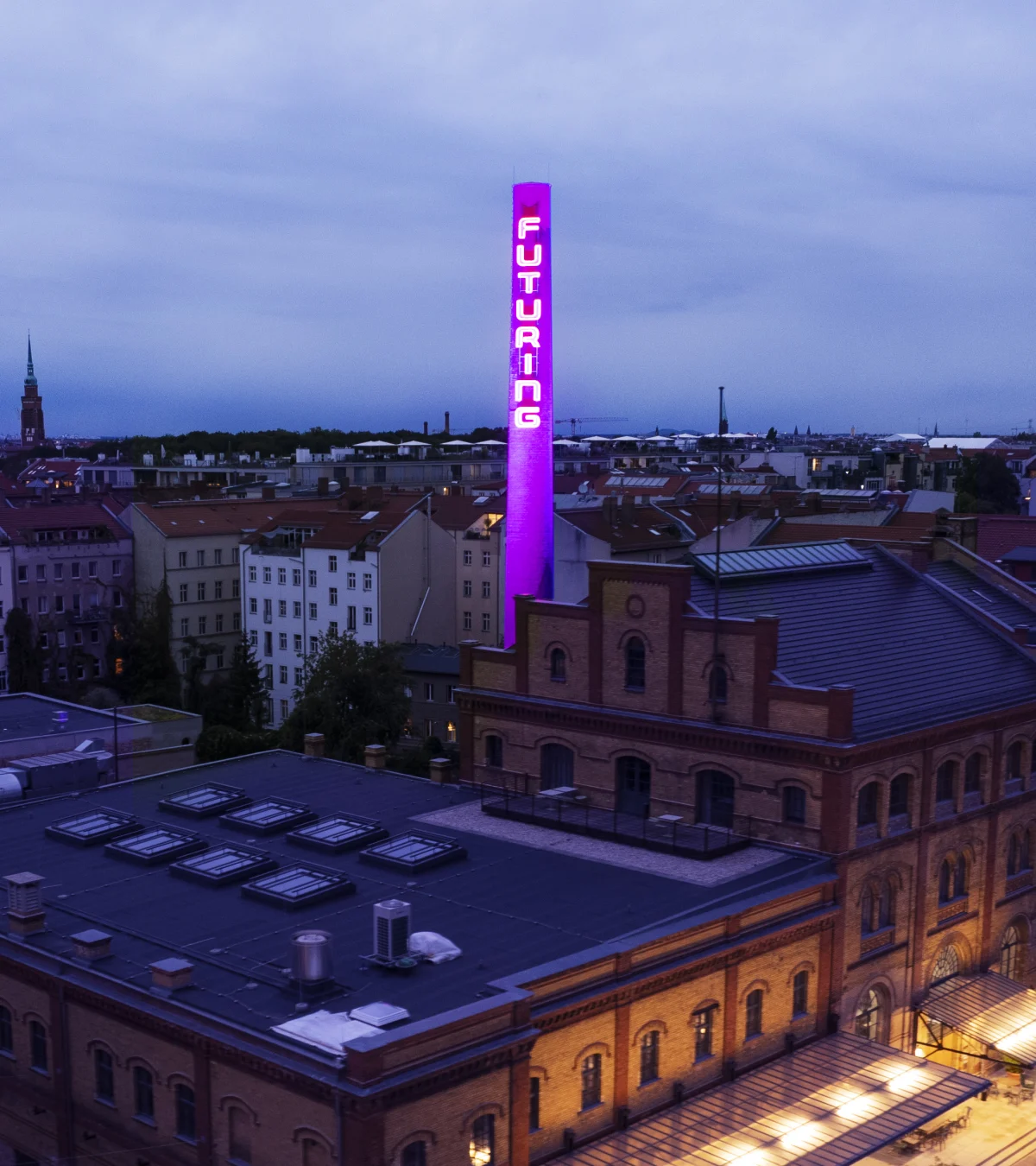
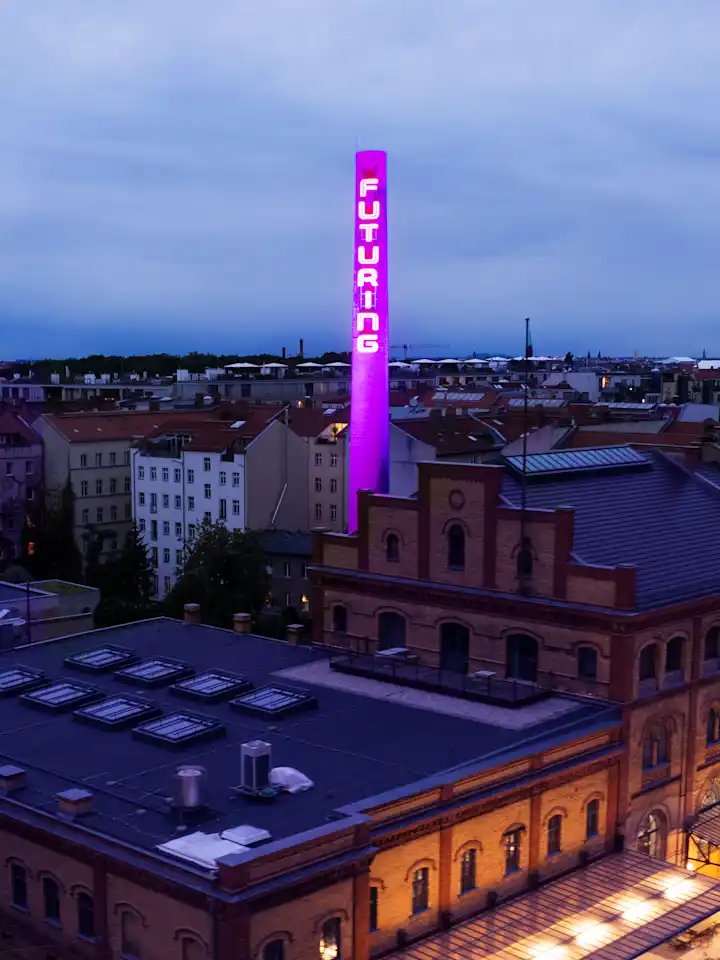
We are inventive
The technical disruption of a startup meets solid values: Ottobock is developing new fields such as neurorehabilitation and quantum sensor technology with research partners around the world. In doing so, we not only want to meet standards in orthopaedic technology, we want to think ahead.
Numerous clinical studies and patents underpin the technological successes of our global network of researchers and developers for innovations in the fields of prostheses, exoskeletons, orthoses and wheelchairs.
A tradition of progress
Each new product draws on our many decades of experience. As a result, we don’t see progress and tradition as a contradiction in terms, but rather as a single, progressive whole. Over the years, we have learned that humans must always remain the ultimate benchmark in our research and development. After all, we measure the quality of our products by the benefits they offer people.
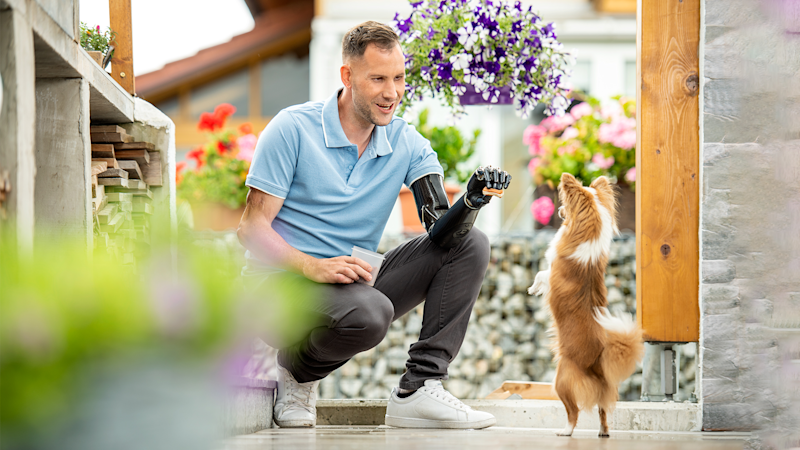
High tech
Our research and development is integrated in an international network of our own sites and scientific institutions.
Interdisciplinary cooperation
The technical expertise and social skills of our employees and partners have a direct impact on the treatment our users receive. They coordinate their work so we can achieve the best results for people.
A cutting-edge reputation
We put our products and company services to the test in international competitions involving a wide range of industries. The awards our company receives show us that we’re on the right path.
Space for ideas
The Ottobock Future Lab on the Bötzow site is an interface to the capital’s creative scene. This is where we’re building our digital future.
The future of orthopaedic technology
We shape the future and drive the digital transformation – from high-tech manufacturing technology to digital treatment processes to smart sensors and the use of artificial intelligence. The needs of our users, patients and customers drive everything we do.
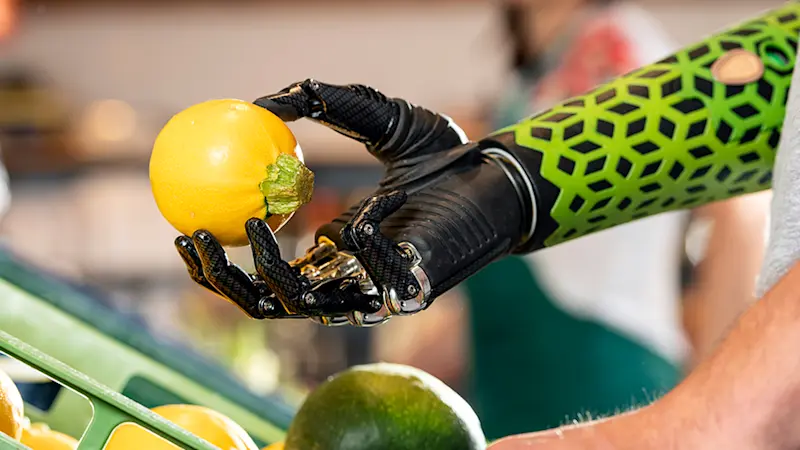
A revolution in patient fittings
iFab (individual fabrication) digitalises the entire fitting and manufacturing process. This makes it possible to produce custom orthoses and prostheses quickly – freeing up more time for the fitting. Sources of errors are also minimised, as the processed data can be tested in a computer simulation and transferred directly to the milling machine and 3D printer.
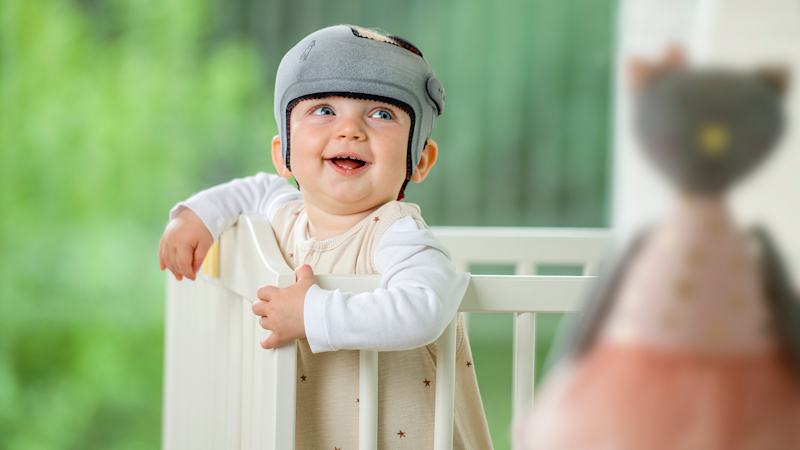
Digitally networked
The Bötzow site in Berlin is Ottobock’s “space for ideas”. Among other things, the Future Lab is developing a digital ecosystem and the networked Patient Care clinic of the future. The aim is to help patients get treatment faster and more easily, make prostheses more customised and connect people via various platforms.
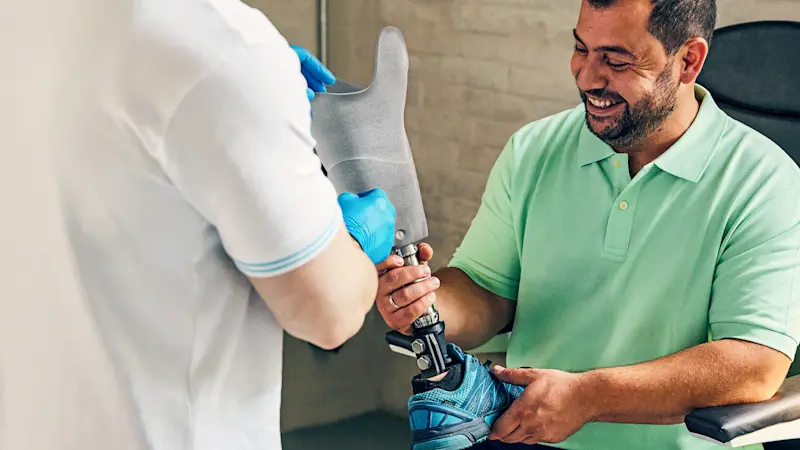