MAN relies on exoskeletons from ‘SUITX by Ottobock’ for workshops
Ergonomic solutions for healthier workplaces
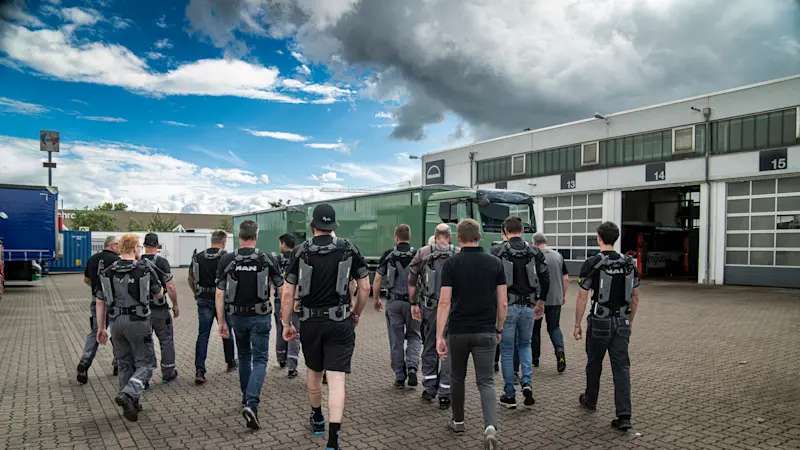
Tuesday, 30 July 2024
MAN Truck & Bus Deutschland GmbH uses exoskeletons from “SUITX by Ottobock” to create more ergonomic workplaces. More than 50 exoskeleton for the shoulder and 25 for the back will be introduced at 20 locations starting in July 2024, accompanied by personal training sessions provided by ergonomics experts. The aim is to reduce employees’ physical strain and promote their health. This is because the maintenance and repair of trucks and buses and the associated lifting and carrying of heavy components or overhead work with tools on lifting platforms are proven to put strain on the back, arms and shoulders and, in the worst case, can lead to downtime. This is precisely where exoskeletons are designed to provide relief.
“At MAN, we chose to use exoskeletons because the social sustainability and health of our employees are particularly important to us. This technology helps us to create ergonomic working conditions and reduce physical strain,” says Dennis Affeld, Chairman of the Executive Board of MAN Truck & Bus Deutschland. “The previous test phase showed that with these exoskeletons, we can also increase satisfaction and motivation of our employees. Here, technological innovations and social responsibility go hand in hand.”
Before introducing the exoskeletons, MAN conducted a pilot study with sensor analysis and feedback forms. The movement situations were analysed for different real workplaces. The study at the Hildesheim, Duisburg and Leipzig sites showed significant relief.These include overhead work with a screwdriving tool weighing five kilograms as well as lifting and carrying goods weighing ten kilograms in the warehouse. The sensor measurements were taken with and without the exoskeleton for the same tasks. The results confirm that the exoskeletons provide significant relief. 70 kilograms less pressure on the lumbar spine per lifting operation and up to 10 Newton meters less torque on the shoulder joints during overhead work, which corresponds to a relief of over 60 percent.
In addition to the measurements, the participating employees answered questions about their experiences with the exoskeletons. The subjective feedback reflects the objective results: Exoskeleton users notice the relief provided to their muscles and joints, and they feel fitter when their work is done.
Employees were also enthusiastic at the introductory event with the ergonomics experts. “My first wow moment came right when I was testing the exoskeleton for the first time, when I noticed someone was helping me so I didn’t have to carry my arms myself anymore,” says Dominik Wirries, a mechanic at MAN Truck & Bus Service in Hanover-Laatzen. His colleague Martin Gökce from the Hamburg-Morfleet site added: “I was actually surprised at how well the exoskeletons provided support. The arm position above the shoulders is significantly relieved.”
MAN relies on the IX SHOULDER AIR exoskeleton and the IX BACK AIR exoskeleton to relieve the workload of its employees. The innovative solutions were developed by “SUITX by Ottobock”. The healthtech company relies on biomechanical systems that operate without external energy (such as electricity). The exoskeletons aim to sustainably reduce physical strain in day-to-day work.
“Our exoskeletons redirect forces in the body, store them and selectively release them again when load peaks occur in the shoulder or spine,” explains David Duwe, Vice President SUITX by Ottobock Europe. “Without the use of batteries, the systems are particularly lightweight and can be worn throughout the day. They can be quickly put on and taken off and adapted to different user heights. With these features, exoskeletons are a key to meeting current challenges in industry and logistics."