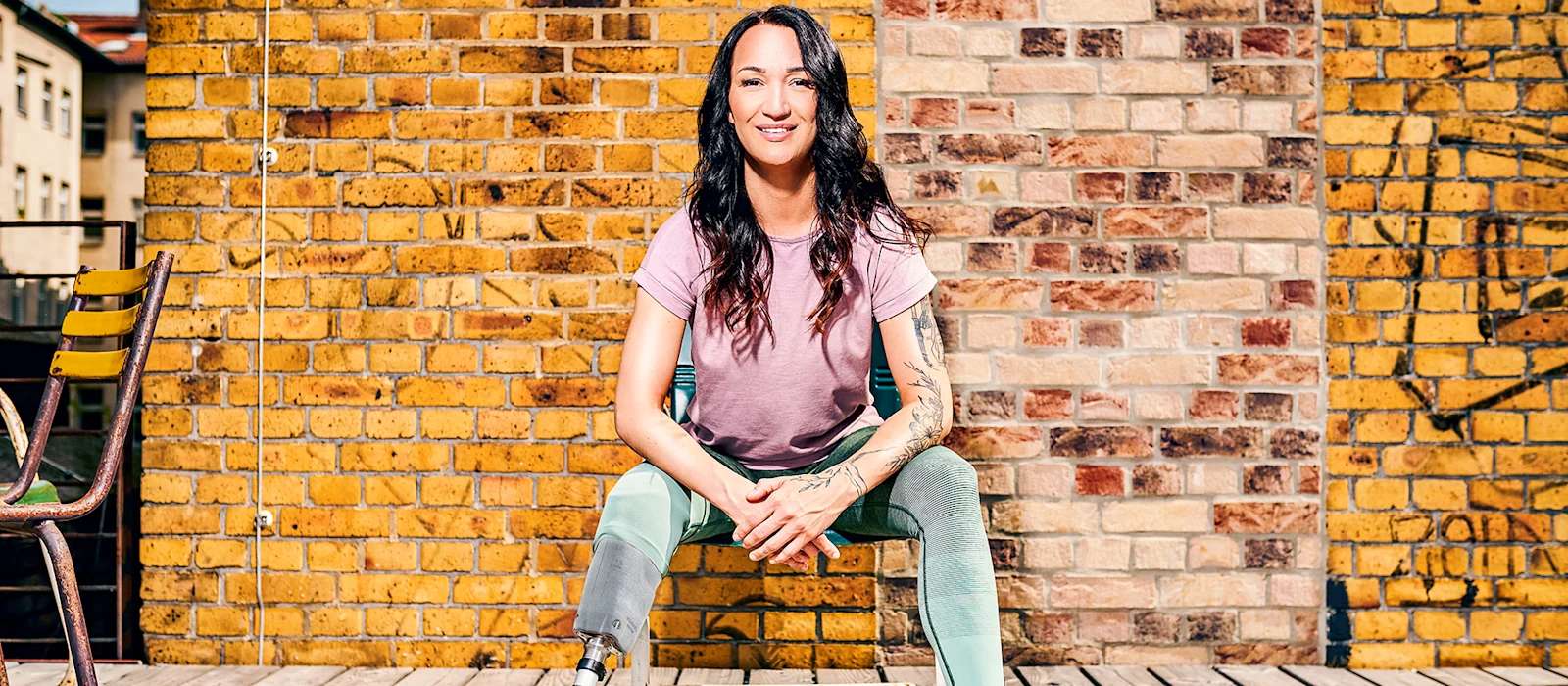
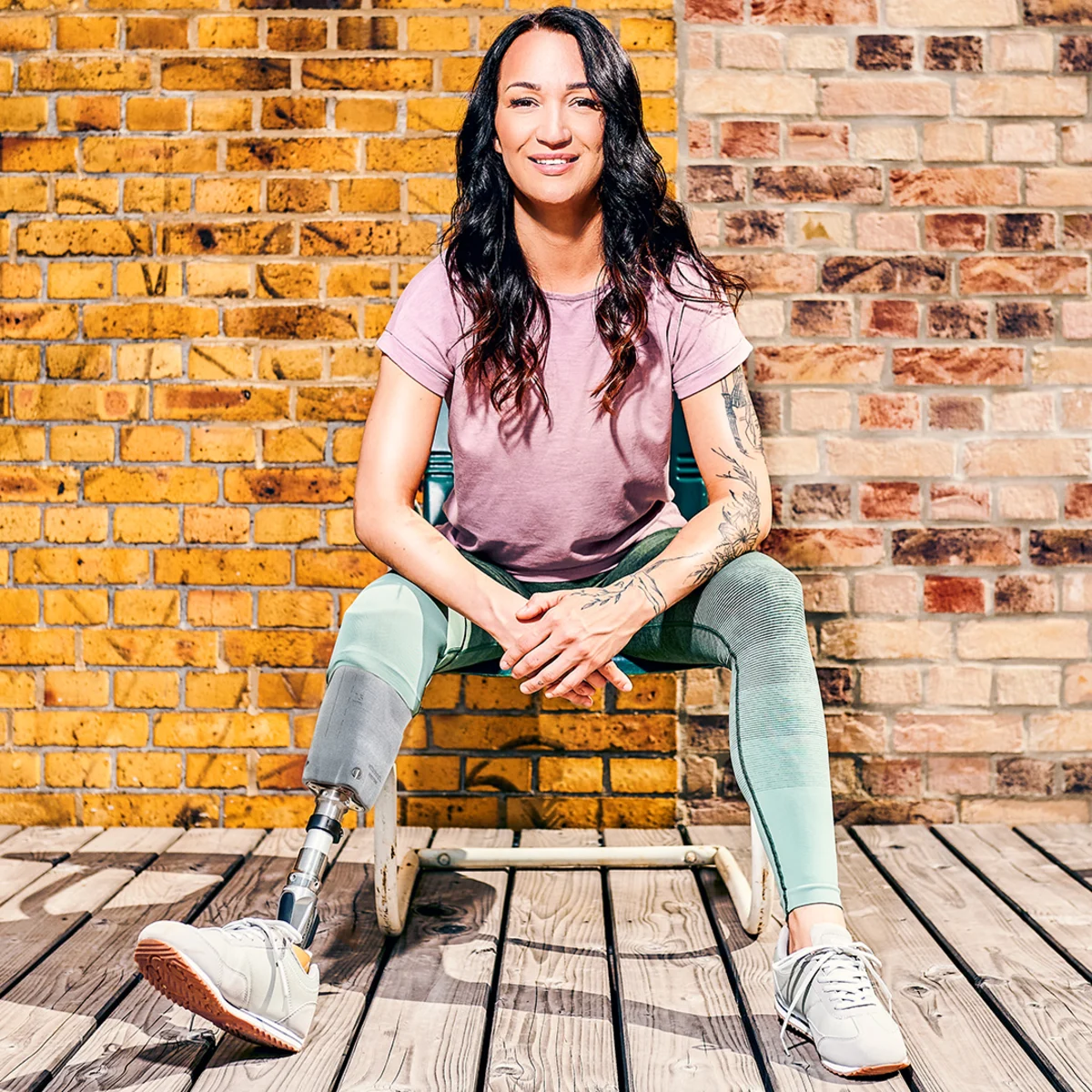
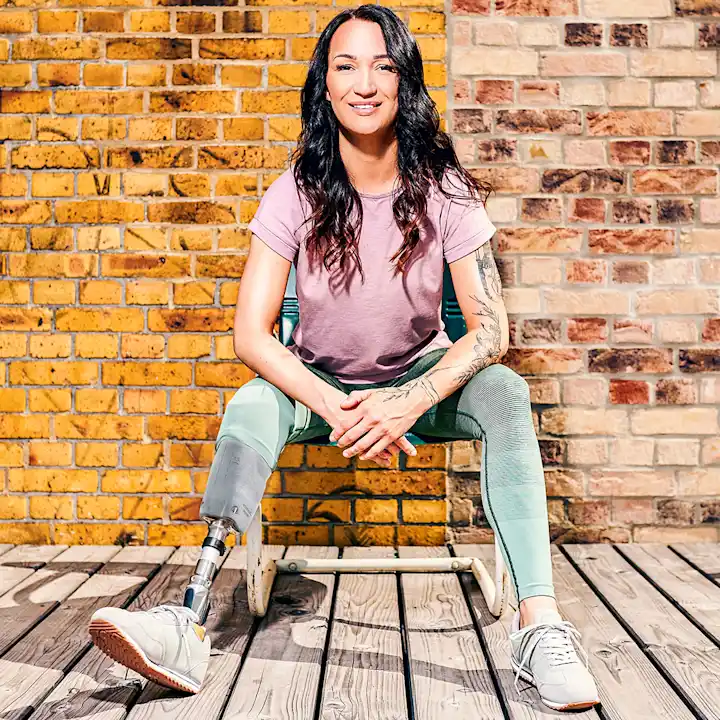
MyFit TT
Der 3D-gedruckte Prothesenschaft für Unterschenkelamputierte von Ottobock, der per Scan generiert wurde. Schnell, sauber und reproduzierbar.
Der 3D-gedruckte Prothesenschaft für Unterschenkelamputierte von Ottobock, der per Scan generiert wurde. Schnell, sauber und reproduzierbar.
MyFit TT: 3D-Druck Schaft
Von jetzt an können OrthopädietechnikerInnen auf Gips verzichten und bei der Versorgung ihrer AnwenderInnen zum 3D-Scanner und -Drucker greifen. Das ermöglicht der erste 3D-gedruckte Prothesenschaft für Unterschenkelamputierte von Ottobock.
MyFit TT bietet eine digitale Komplettlösung an: von Scannen, zur Software bis zum 3D Druck.
Inspiriert von der Struktur eines menschlichen Knochens, schufen die EntwicklerInnen einen Schaft, der bei hoher Stabilität mit wenig Material auskommt. Möglich macht das ein 3D-Druckverfahren auf Pulverbasis. Nylon-Pulver gibt dem Schaft genügend Flexibilität für das An- und Ausziehen. Gleichzeitig ist es robust genug für den täglichen Gebrauch.
Digitalisierung macht Branche zukunftsfest
Mit der neuen Technologie entfällt die manuelle Fertigung – insbesondere der Gipsabdruck des Stumpfs, die Korrektur des Gipsmodells zur Schaft-Formerstellung bzw. Hilfsmittel-Erstellung sowie die eigentliche Fertigung des finalen Schaftes. Gleichzeitig kann der additiv gefertigte Schaft mit der Qualität eines konventionell gefertigten Schaftes mithalten. 3D-gedruckte Prothesenteile verfügten in der Vergangenheit häufig nicht über die gewünschte Stabilität. MyFit TT löst diesen Anspruch für eine vollständig digitalisierte Versorgung. Dieser digitale Versorgungsprozess macht das Patientenerlebnis im Sanitätshaus damit nicht nur angenehmer, er verringert auch den Arbeitsaufwand. So bleibt mehr Zeit für direkte Gespräche.
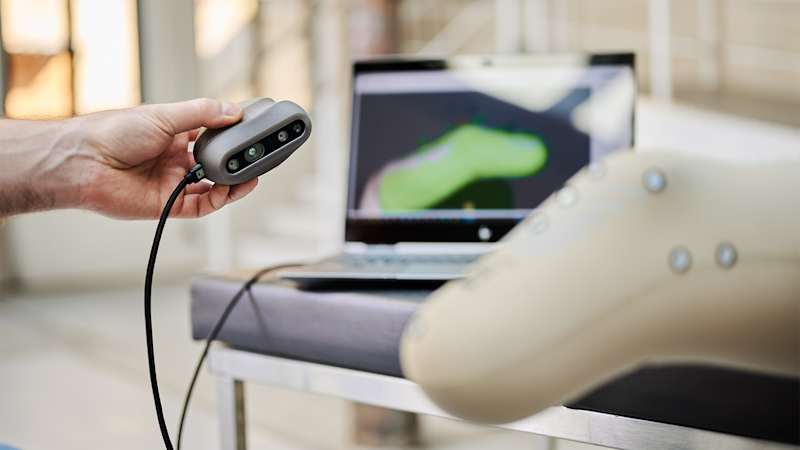
Vorteile der additiven Fertigung
Digitaler Zwilling
Eigenheiten am Stumpf, wie knöcherne Strukturen, lassen sich markieren, mit dem Scanner erfassen und in der Modifikationssoftware einblenden.
Nachvollziehbar
Alle Schritte der Bearbeitung werden dokumentiert und lassen sich und reproduzieren. Auf Knopfdruck können sie angepasst und rückgängig gemacht werden.
Ressourcenschonend
Der herkömmliche Gipsabdruck entfällt. Stattdessen wird der Schaft ohne Modell direkt gedruckt, wodurch weniger Müll entsteht.
Zeitersparnis
Mit der neuen Technologie entfallen einige Schritte der manuellen Fertigung. Dadurch haben OrthopädietechnikerInnen mehr Zeit für die AnwenderInnen.
Scannen. Modellieren. Drucken. Passgenauer Sitz mit weniger Zeitaufwand.
- 3D-Scan: Das Körperteil wird mit einem Scanner rundum (360°) erfasst. Diese Methode ist angenehmer und schneller als ein Gipsabdruck.
- Digitale Modellierung: Durch die Bearbeitung des Scans in der Software kreiert die Orthopädietechnikerin bzw. der Orthopädietechniker die Form des späteren Schaftes.
- 3D-Druck: Im 3D-Drucker wird der Schaft durch ein sogenanntes Pulververfahren hergestellt.
- Anprobe: Der bzw. die OrthopädietechnikerIn überprüft die Passform und den Tragekomfort.
Mit MyFit TT den Bedürfnissen gerecht werden
"Der Prothesenschaft muss sitzen"
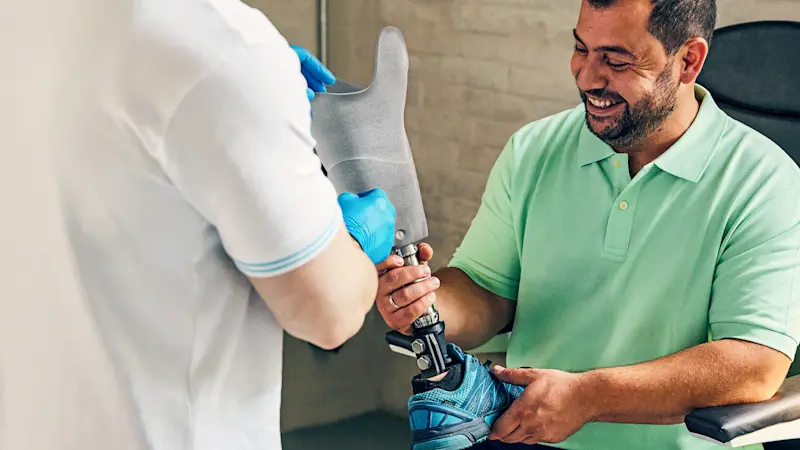
Beytullah Demir ist einer der ersten Träger des MyFit TT Schaftes aus dem 3D-Drucker von Ottobock. Er verlor 2012 seinen Unterschenkel bei einem Arbeitsunfall. Damit seine Prothese gut sitzt und am Stumpf nicht schmerzt, ist ein perfekt angepasster Schaft nötig: das Bindeglied zwischen Mensch und Technik. Dieses muss sitzen, wie ein Handschuh. Heute geht Beytullah wieder arbeiten, spielt Fußball und trainiert eine Mannschaft in seinem Heimatort.
Du bist gerne auf dem Fußball-Platz – mit Prothese. Was bedeutet das nach der Amputation für dich?
Ich habe schon seit klein auf Fußball gespielt. Heute bin ich im selben Verein wieder Trainer und Spieler. Dass ich das nach der Amputation geschafft habe, ist ein Wunder.
Worauf bist du noch stolz?
Nach dem Unfall traten die wichtigen Sachen im Leben für mich in den Vordergrund. Ich bin wacher geworden, weil man merkt, dass das Leben von heute auf morgen enden kann. Ich habe ein Haus gekauft, meine Freundin geheiratet und Kinder bekommen. Sie wollte es - zu dem Zeitpunkt waren wir neun Jahre zusammen und ich fand es zuvor immer zu früh. Wir streiten auch nur noch über Kleinigkeiten. Ich lebe heute einfach glücklich.
Wie hast du erfahren, dass der Unterschenkel amputiert werden muss?
Ich bin im Krankenhaus aufgewacht und weiß ehrlich gesagt nur wenig von den ersten Tagen auf der Intensivstation. Ich dachte, ich liege in der Nähe von Höxter im Krankenhaus, doch die Schwester sagte, dass ich in der Uniklinik in Göttingen bin. Ich wusste: Nach Göttingen kommst du nur, wenn du was Ernstes hast. Der Chefarzt sagte, dass ich keine Blutversorgung mehr im Fuß habe und er die Amputation empfiehlt. Er sah keine Heilung mehr.
Wie hast du darauf reagiert?
Ich wollte erst eine Klinik finden, die meinen Fuß rettet. Aber die Wahrscheinlichkeit einer Blutvergiftung war viel höher. Nach einer Odyssee durch einige Krankenhäuser musste ich eine Entscheidung treffen. Ich habe mir meine Haare vom Kopf gerissen, weil ich so verzweifelt war. Zum Glück sind auch die Fenster in der UMG geschlossen, weil mir Gedanken kamen, zu springen. Dann habe ich mich entschieden, meinen Unterschenkel zu amputieren. Sie haben mich in den OP gefahren und ich habe angefangen zu weinen. Weil ich wusste, wenn ich rauskomme, komme ich ohne Bein raus. Ich habe mich dann von meinem Bein verabschiedet.
Wie hast du die Zeit nach der Amputation erlebt?
Ich habe die Decke hochgehoben und es begann eine psychisch schlimme Phase. Aber mein Arzt war Tag und Nacht für mich da. Er hat zu mir gesagt: „Du hast zwei Möglichkeiten, entweder du stehst auf und kämpfst um dein Leben - oder du kommst morgen früh direkt nebenan in die Psychiatrie.“
Was hat das mit dir gemacht?
Nach dem Gespräch dachte ich mir: Komm, steh auf! Aus dem Fenster kannst du immer noch springen. Ich habe wieder Menschen in mein Leben gelassen. Mein Zimmer sah aus wie ein Blumenladen. Es waren viele Menschen da, von denen ich es nie erwartete hätte. Letzten Endes habe ich jeden von ihnen gebraucht. Das hat mich gestärkt; ich habe angefangen, wieder am Leben teilzunehmen.
Wie war die erste Zeit mit Prothese?
Ottobock kam zu mir nachhause und ich wurde erstversorgt. Dann war ich sechs Wochen stationär auf Reha. Dort habe ich tragischere Schicksale gesehen als meines, und gemerkt, dass ich alles wie früher machen können will. Nach drei Wochen habe ich die Krücken abgegeben. Ich habe dann im September 2013 wieder angefangen, Vollzeit im alten Job zu arbeiten.
Du wurdest mit einem 3D-gedruckten Schaft versorgt. Wie ist der Unterschied im Vergleich zum herkömmlichen Gipsabdruck und Schaft?
Ich war der erste Anwender, der in Duderstadt gescannt wurde. 3D-Druck ist für mich genial, weil es angenehmer ist ohne den ganzen Gips - auch für die Umwelt. Mein Techniker scannt mich und paar Tage später bringt er mir den Schaft. Ich springe rein und es passt. Ich hätte nichts dagegen, wenn ich meine Prothesen alle mit 3D-Druck bekommen könnte. Es ist schneller fertig, es ist sauberer und bequemer.
Wie kann man sich das vorstellen, wie viel schneller ist der 3D-Druck?
Mit dem Gipsabdruck ist der Techniker in einer halben Stunde durch. Mit 3D-Scanning in zehn Minuten, wenn überhaupt - nur einmal rumgehen.
Fühlt sich so ein Schaft aus dem 3D-Drucker anders an?
Ich kann mit meinem Schaft besser in die Beuge gehen. Für mich ist es wichtig, dass der Schaft gut passt. Ansonsten bringt die beste Prothese nichts. Alle Schäfte, die mit 3D-Druck gefertigt wurden, haben richtig gut gesessen, richtig fest. Wie angewachsen. Ich bin sehr zufrieden und finde ich es ist eine angenehme Sache.
Ansprechpartnerin
Weitere Themen
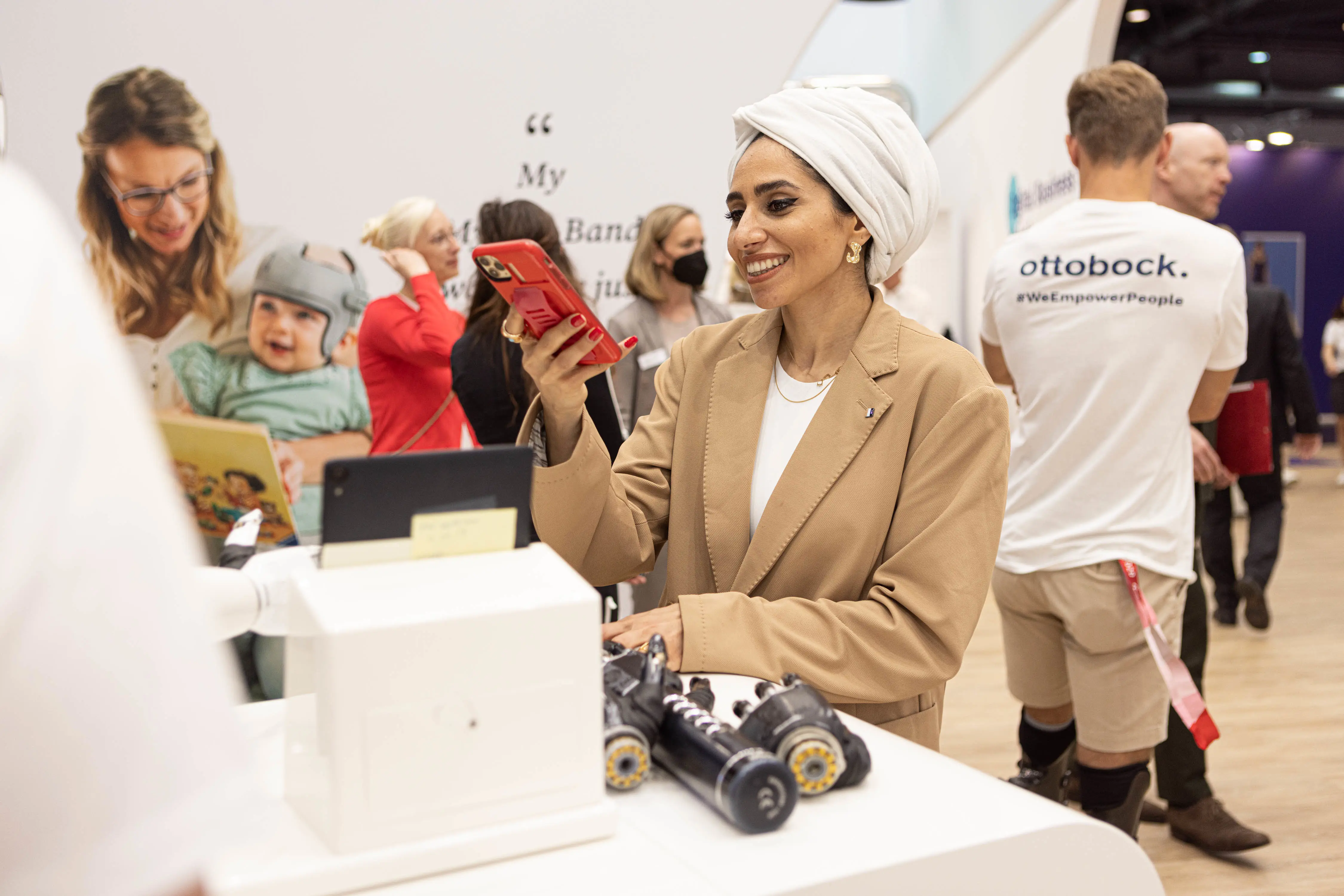
Medieninformationen
Sie möchten mehr über unsere Produkt-Highlights erfahren? Sie benötigen hochauflösende Bilder für Ihr Medium? Für Journalistinnen und Journalisten haben wir hier Produktinformationen und Bildmaterial zusammengestellt.
Sie möchten mehr über unsere Produkt-Highlights erfahren? Sie benötigen hochauflösende Bilder für Ihr Medium? Für Journalistinnen und Journalisten haben wir hier Produktinformationen und Bildmaterial zusammengestellt.
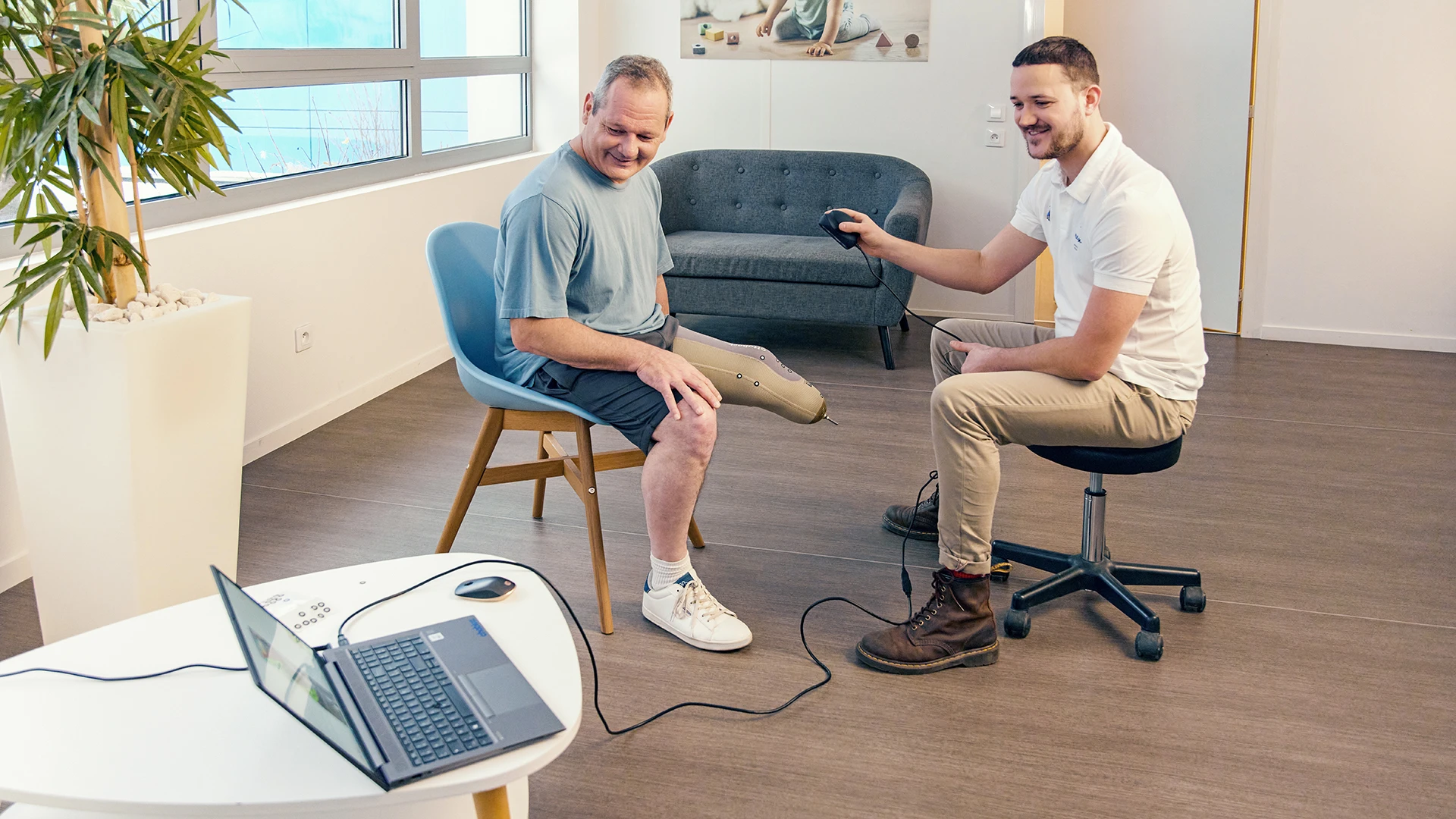
Wie 3D-Scanner und -Drucker die Patientenversorgung revolutionieren
Schnell und maßgeschneidert produzieren – das ist die Zukunft der Orthopädietechnik. Das iFab revolutioniert den gesamten Versorgungs- und Fertigungsprozess.
Schnell und maßgeschneidert produzieren – das ist die Zukunft der Orthopädietechnik. Das iFab revolutioniert den gesamten Versorgungs- und Fertigungsprozess.
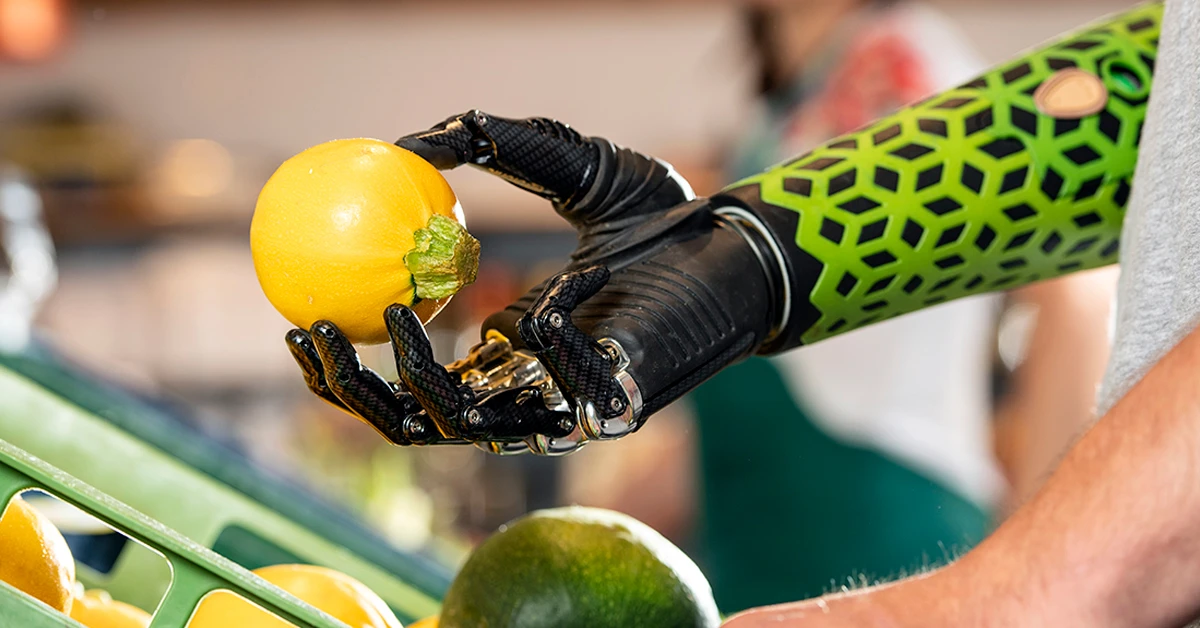
Myo Plus Mustererkennung
3 Ergebnisse von insgesamt 3